Description
BIG BAG FILLING - Containment and stability
The FlowMatic® 02 system incorporates an inflatable containment seal and height adjustable big bag hanging hooks. The height of the hooks can be adjusted with a pneumatic cylinder which provides optimal tensioning of the FIBC during filling operation. The pneumatic tensioning cylinder also enables the packaging of big bags with varying dimensions. The filling head is designed with a double casing to ensure prevention of back pressure and dust emissions to the outside atmosphere.
The FlowMatic® 02 big bag filling station has a filling rate of 10 to 20 bulk bags per hour.
The width of the hanging hooks is manually adjustable, which further administers proper tensioning of the big bag and accommodation of varying FIBC dimensions. Therefore, both height and width adjustments ensure optimal and stable filling operation. The inflatable seal fixes the big bag spout to the station during the filling process and allows high flow rates to be processed.
The automatic height adjustment of the forks, with a tension cylinder, enables a tensioning of the big bag. This device ensures an optimal and stable filling. The inflatable seal seals the filling sleeve during the filling process and allows high flow rates to be processed.
-
Ease of integration5
-
Ease of implementation5
-
Dosage accuracy3
Equipment advantages
- Width adjustable hooks for optimal filling of all dimensions of big bags
- Inflatable seal to ensure dust containment and facilitate high flow rates (prevent back pressure)
- Tension cylinder to facilitate shape of the big bag during filling operation and for safer handling operations
- Removal of the big bag possible by forklift or pallet truck
Media
View our equipment in photos
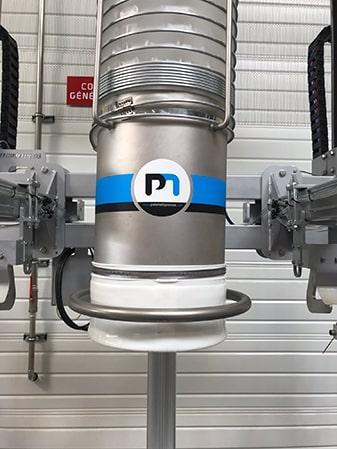
FlowMatic® 02 - Palamatic Process
Big bag Conditioner FlowMatic® 02 by Palamatic Process.
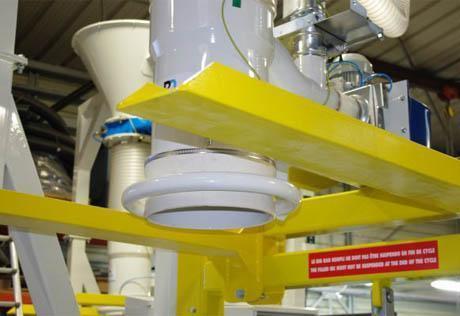
Filling big bags
Inflating seal on big bag packaging station.
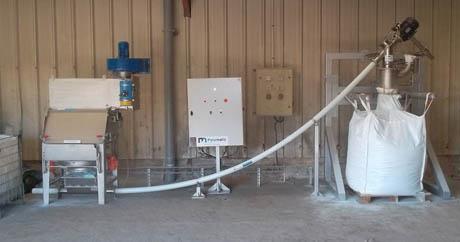
Big bag filling line
The Sacktip® SE bag emptying screening station feeds the big bag filling station.
The powder or bulk material is transported undamaged by an easy-to-clean conveying screw. To prevent the formation of agglomerates, a vibrating screen is installed beneath the bag emptying station.
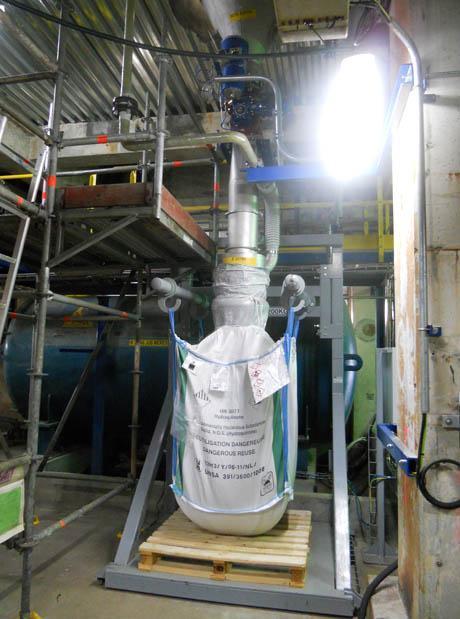
Big bag packaging - FlowMatic® 02
Filling a big bag with a rotary gate valve.
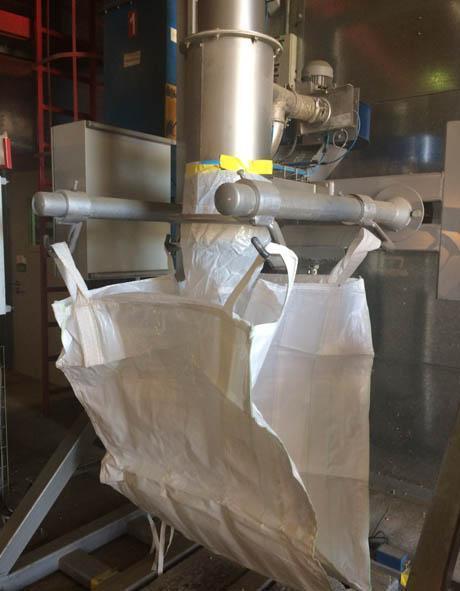
Bulk handling - Big bag filling system
The forks of the big bag loading station are equipped with adjustable forks for optimum filling of all types of big bags.
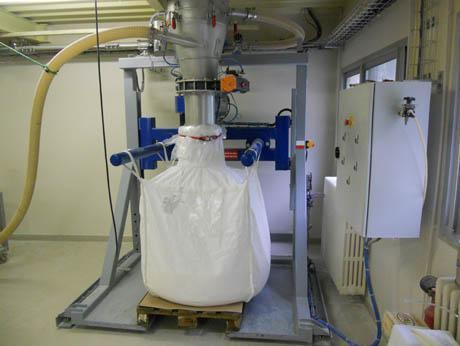
FlowMatic® 02 on a pneumatic conveying line
The round forks of the big bag filling station are adjustable in width, facilitating big bag removal.
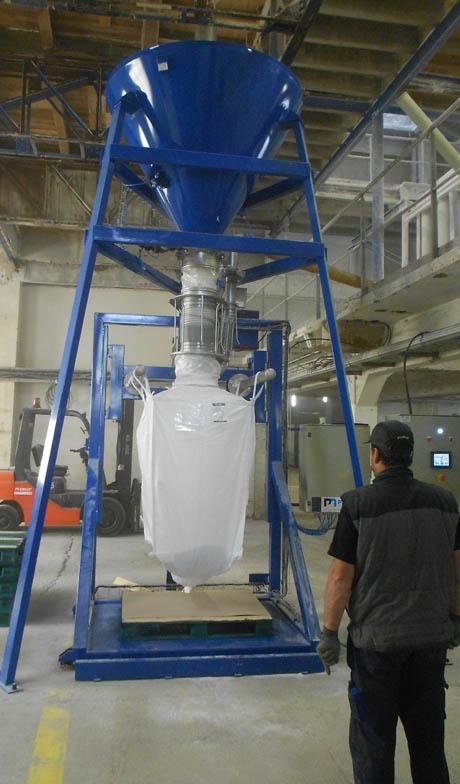
FlowMatic® 02 with hopper
Filling big bags with fluorinated derivatives on an ethanol production line.
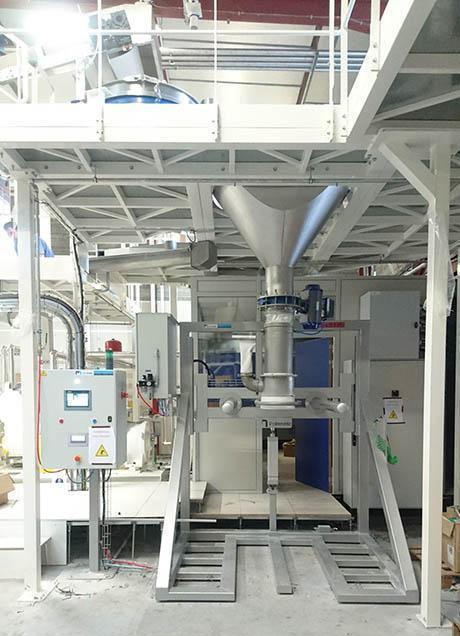
Bulk loading in big bags
This application concerns a station for conditioning granules in big bags from a buffer hopper. The big bag packaging station is equipped with a weighing system controlled by a slide valve to stop the flow of material once the target weight has been reached. The filled big bag is evacuated by an electric pallet truck.
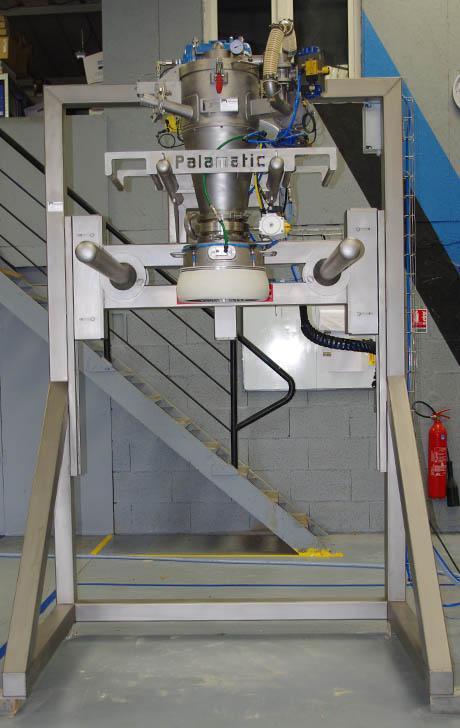
Big bag filling system on a pneumatic conveying line
The vacuum conveying cyclone is used to feed metal powders into the big bag filling station.
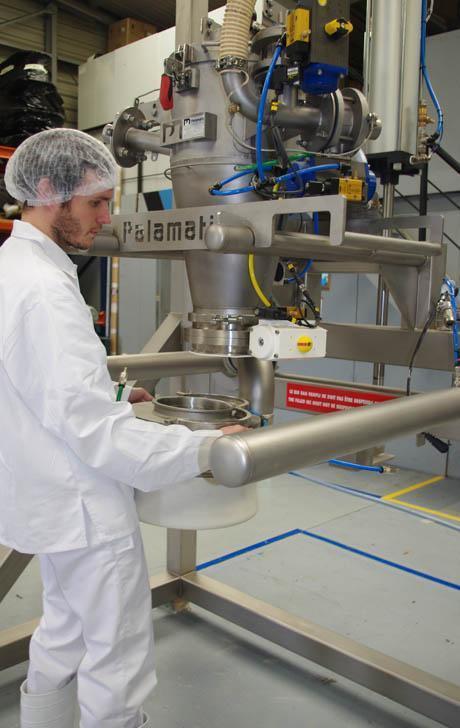
FlowMatic® 02 big bag conditioner
FlowMatic® 02 big bag filling station with hygienic design. A rotary valve is integrated to regulate the filling rate.
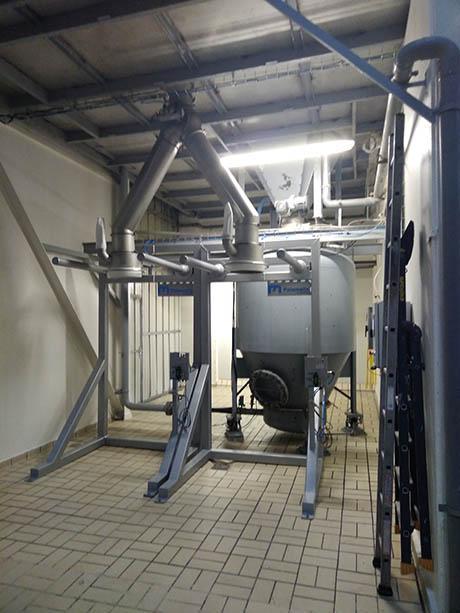
Double big bag filling station
Filling of big bags with bulk materials for the manufacture of products for the chemical industry.
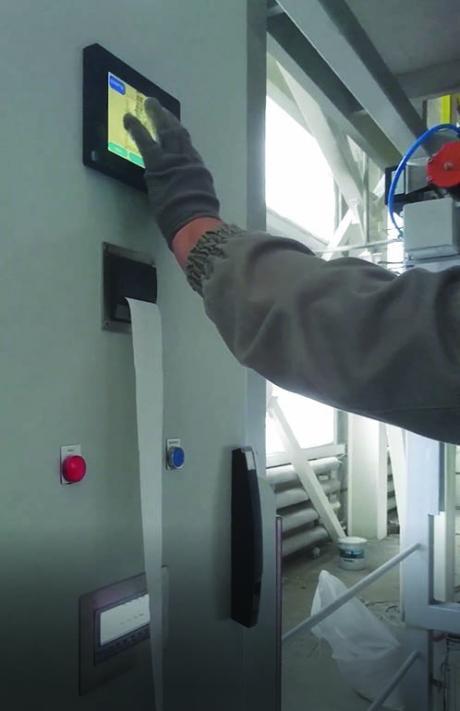
Automation of a big bag filling station
Automated filling line for FlowMatic® 02 barite in big bags.
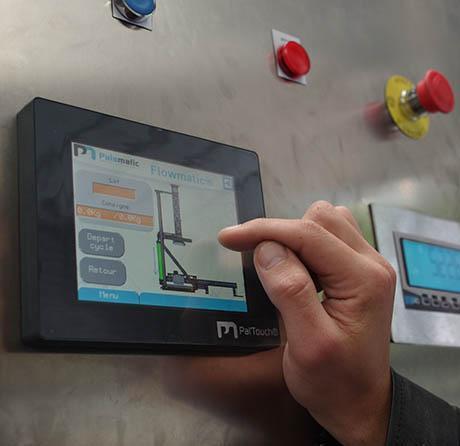
Pal'Touch technology
PLC on a big bag packaging line using corn starch.
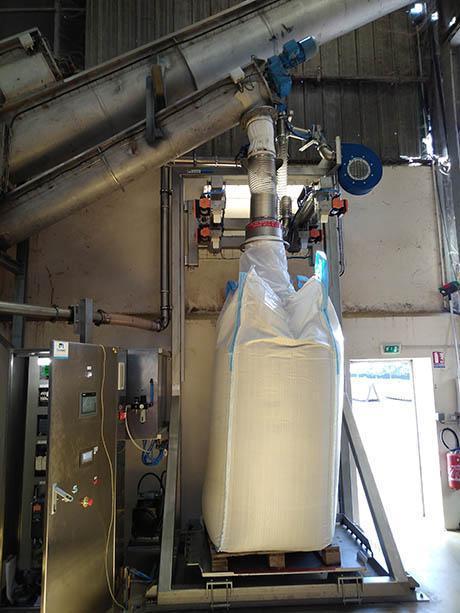
Screw conveyor for big bag filling
Big bag loading station at a calcium carbonate plant.
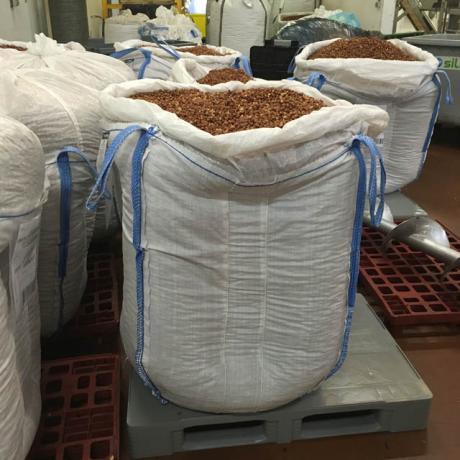
Bulk handling - Big bag filling
Food flavorings production line.
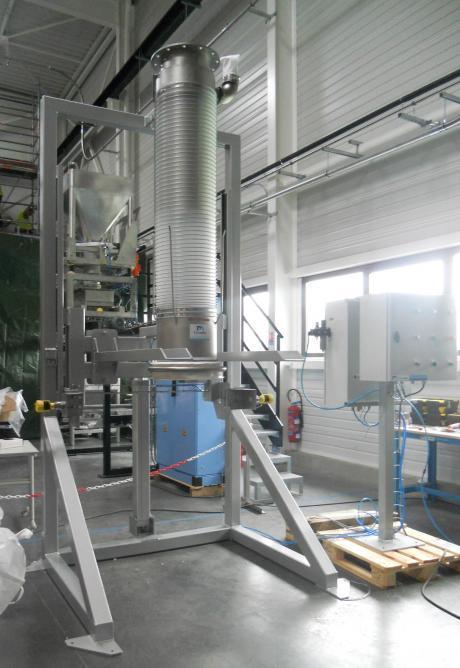
Level sensor on big bag filling station
FlowMatic® 02 filling a big bag with iron sulfate.
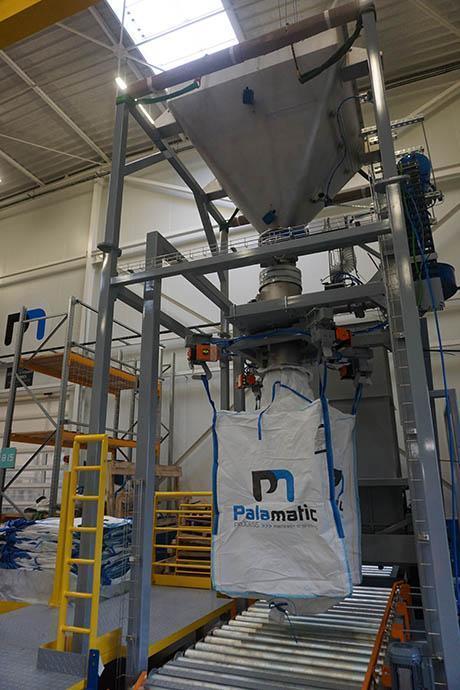
Big bag filling line
Big bag filling station on an industrial glue production line.
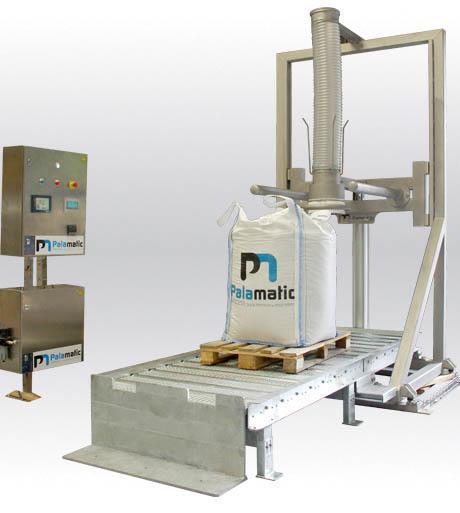
Big bag filling with roller conveyor
Plasterboard manufacturing process.
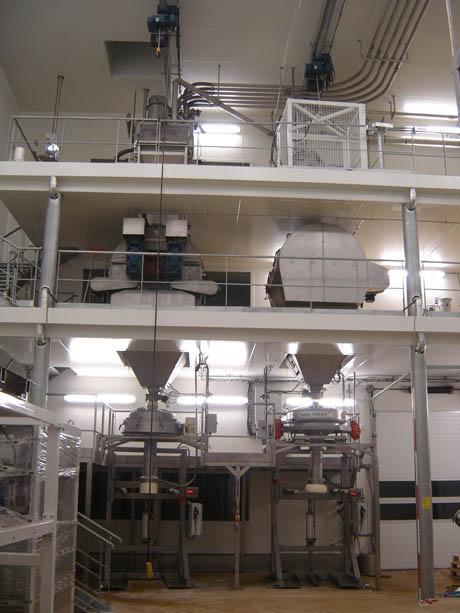
Big bag packaging process line
Additive blending line for the production of flavors for animal feed.
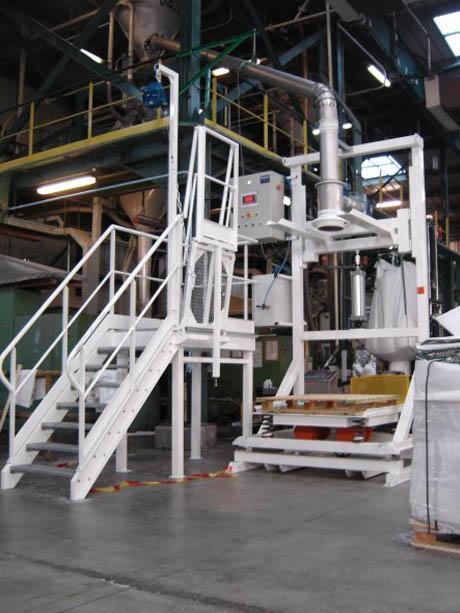
Packaging platform for big bags
Maltodextrin big bag packaging station.
Features
Technical specification
Rate | 10 to 20 big bags/h. |
---|---|
Capacity | 2 tons/big bag |
Manufacturing materials | Painted steel, 304L stainless steel |
Installed power | 0.2 kW |
Compressed air consumption | 0.9 Nm³/h. |
Dust removal rate | 300 m³/h. |
Finishing touches: RAL 9006, microblasted, electropolishing
Operating pressure: 6 bar
TOR input: 0
TOR output: 2
Maximum dimensions of the big bags: 1,550 (l) x 1,550 (L) x 2,400 (H) mm
U-shaped forks: enable the removal of the big bag by the handles (optional)
Integrated equipment to the FlowMatic® 02 model:
- Round forks for attaching the handles of the big bag: offers an easier sliding of the handles of the big bag.
- U-shaped forks for attaching the big bag handles: allows the big bag to be evacuated directly through the handles using a forklift truck (no pallet is used).
- Support structure: the structure is manually height adjustable to adapt to all types of big bag
- Width adjustment: the center distance of the forks is width adjustable to optimize the filling operation but provides an increased stability of the flexible container on the pallet.
- Inflatable seal: The inflatable seal ensures an airtight connection between the filling head and the big bag during its filling.
- Filling head: the filling head is designed in a double casing for volume balancing. The charged air is evacuated through the degassing line which can be connected to the dedusting network.
- Tension cylinder: the pneumatic cylinder is installed on the deck of the suspension forks. It allows to bring the system for attaching the handles of the big bag to ergonomic height, to adjust to the different big bag heights and to give an optimal shape to the big bag thanks to the permanent tensioning during the whole conditioning phase. The big bag is perfectly filled without any risk of pocketing and can be handled safely, without any risk of it tipping over.
Case studies
CASE STUDIES WITH THIS EQUIPMENT
Wheat bran and lime premix line
Processed powders: wheat bran and lime with a bulk density of 0.4 to 1 kg/m³ - Wheat bran and lime premix line - Estonian engineering company specialized in the design of industrial operations for the...Food and Animal Feed
Seeds packing line
Processed products: corn seeds - Seeds packing line - Installation for conditioning corn seeds in big bags. The big bag filling station is supplied upstream via a slide gate valve and a flexible...Chemical
Pharmaceutical contrast products
Processed powder: pharmaceutical active ingredient - Pharmaceutical contrast products - The customer is a pharmaceutical factory manufacturing injectable substances for the medical sector.Fine chemical
Loading drums and big bags
Processed powder: chromium powder - Drum and big bag loading - The objective is to screen and package in big bags or drums chromium powder with an integrated dosing system.Chemical
Refiom processing line
Processed products: fly ashes and ash embers - Refiom processing line - Big bag filling in thermal power plant in a household waste incineration plant.Energy
Transfer and bagging of plastic parts
Products treated: caps for medical use - Transfer and bagging of plastic parts - The customer is a manufacturer of needle caps for the pharmaceutical industry.Fine chemical
Grinding and packaging of finished products
Processed products: dried insects - Grinding and packaging of finished products - Workshop for processing and packaging products for the animal nutrition sector.Food and Animal Feed
Repackaging in drums and small big bags
Processed powder: Dextrose Anhydride - Repackaging in drums and small big bags - The installation is a complete turnkey line allowing the repackaging of dextrose from big bags into plastic drums or...Fine chemical
Unloading and filling of manganese dioxide big bags
Processed powder: lithium nickel potassium oxide - Unloading, filling of big bags and transfer of material - The objective of this installation is to protect the operators with equipment designed to...Energy
Process for mixing dry ingredients
Processed Materials: Granulated Sugar, Rebaudioside M, Cocoa Powder and various minor ingredients - Process for mixing dry ingredients - The new facility expansion project required the capabilities of...Food and Animal Feed
Packing of 1-ton big bags for the containment of dust fumes
Processed powder: zirconium - Big bag packaging line below the dryer - Dust containment - Big bag compactor with screw conveyor.Chemical
Optimizing Bulk Bag Discharge with BFM® Fitting Connections
Powders handled: Pharmaceutical excipients and food ingredients - Optimizing Bulk Bag Discharge with BFM® Fitting Connections - Bulk Bag Discharge Solution with BFM® Fitting ConnectionsFood and Animal Feed
Receive our quotation in 3 clicks!