Description
BIG BAG FILLING - AUTOMATIC PACKAGING IN GROSS WEIGHING
The FlowMatic® 04 big bag filling system is the complete solution for automatic conditioning of big bags in gross weighing operations. This FlowMatic® 04 model is designed for continuous use at high flow rates of 20 - 40 big bags/hour.
The FlowMatic®04 big bag filling automation equipment incorporates an inflatable dust containment seal and a height-adjustable structure. The adjustable structure makes it possible to package big bags of various dimensions and according to the characteristics of the big materials.
-
Automation5
-
Rate3
-
Overall dimensions3
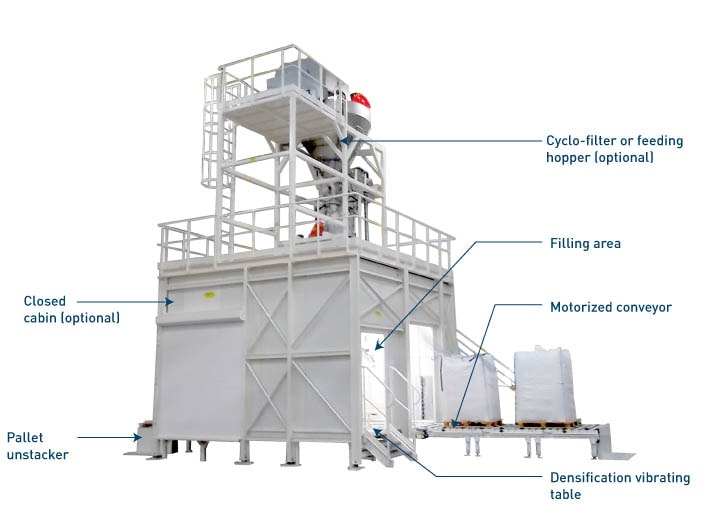
Operating procedure:
1. Automatic feeding of empty pallets via a belt conveyor
2. Installation of the big bag on the filling station
3. The bulk bag spout is connected to the inflatable seal for dust containment and stability
4. Tensioning and height adjustment of the big bag by pneumatic cylinder
5. Inflation of the big bag for preforming and efficient filling
6. Switch from the inflation system to the dust collection exhaust
7. High rate filling commences
8. Bulk Bag is gradually lowered onto the pallet. Bottom of the big bag is formed to promote stability for handling
9. Vibration table works intermittently during filling operation to densify and deaerate the material.
10. Gross weight management with a low speed switch to adjust the final dosing stage
11. End of filling: lowering of the filling head, deflation of the seal and automatic removal of the big bag loops
12. Automatic removal of the big bag to the storage area by belt conveyor
Automatic gross weighing and big bag filling
The complete solution for automatic conditioning of big bags, FIBCs, super sacks, jumbo bags and bulk bags in gross weighing operations. This model is designed for continuous use at high flow rates of 20 - 40 big bags/hour.
The automated big bag filling FlowMatic 04 integrates all the necessary options for big bag packaging with minimum operator intervention: inflatable seal, big bag hanging deck with pneumatic cylinder height adjustment, big bag pre-forming fan, weighing and dosing of big bags, optional commercial weighing load cells, vibrating densification table, pallet unstacker, belt conveyor, etc.
Equipment advantages
- Conveyor and buffer storage to achieve high rates
- Automatic dosing and weighing
- Automatic removal of bulk bag loops
- Pallet unstacker with a capacity of 15 multi-format pallets
Media
View our equipment in videos
Automatic big bag filler
Big bag filling station - Flowmatic® 04
3D big bag filling system - Flowmatic 04
Bulk bag filling range
Big bag filling system FlowMatic 04
Big bag filler - Flowmatic® 04
View our equipment in photos
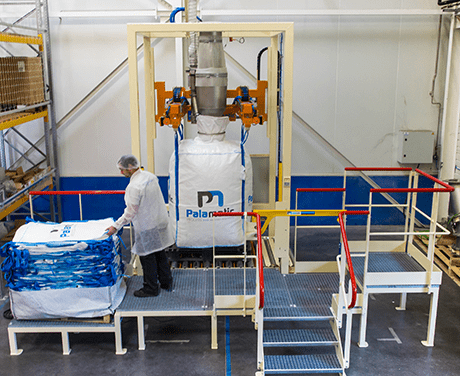
Big bag packing
Loading of tobacco dust in big bag.
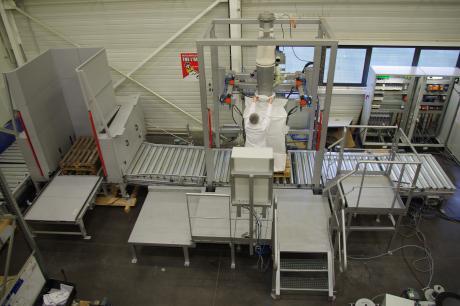
Automatic conditioning with gross weighing
FlowMatic® 04: automatic packing line of urea in big bags: dosing, packaging and conveying.
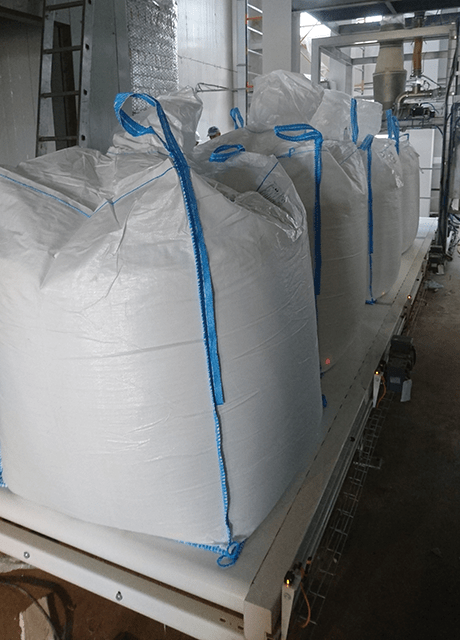
Industrial production line for big bags filling
Belt conveyor on a packing line for big bags of sugar.
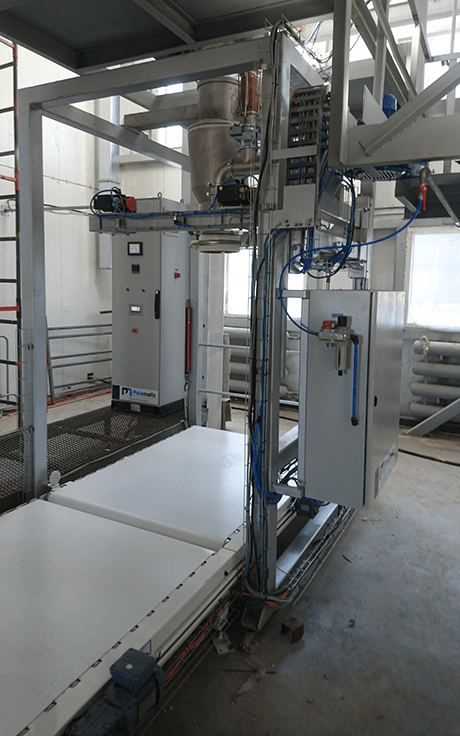
Packaging station for big bags filling
Automatic big bag filling line for white sugar packing.
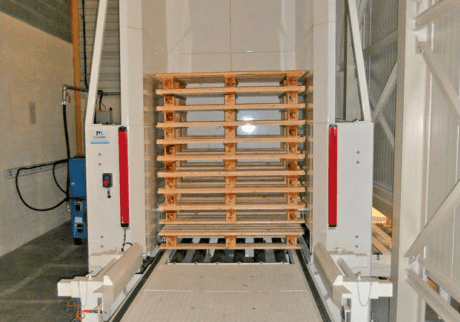
Pallet unstacker
The pallet unstacker is used to automatize the big bag filling station.
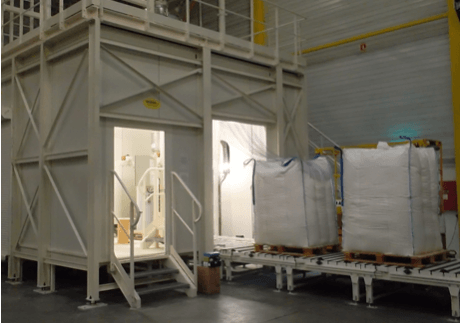
Big bag removal roller conveyor on fibc filling station
Starch discharge in trucks for automatic packing of big bags in the Atex zone.
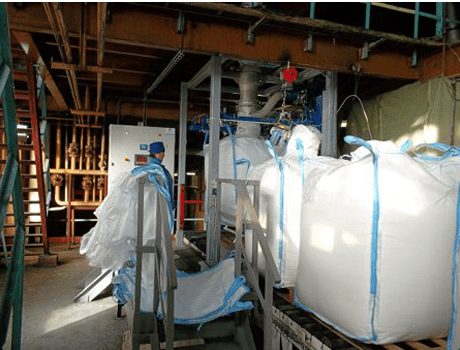
Bulk bag filling system Palamatic process
Hygienic big bag packing station for the preparation of infant milk powder.
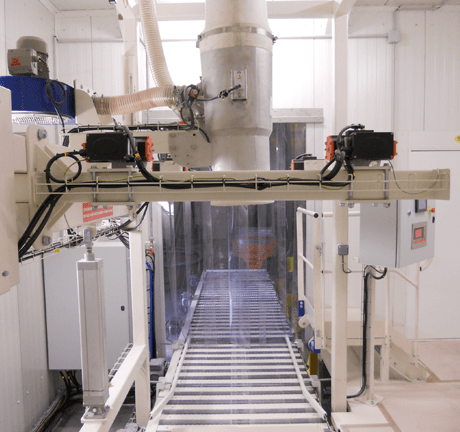
Output fibc automatic line after filling system
Packing station for handling food starch.
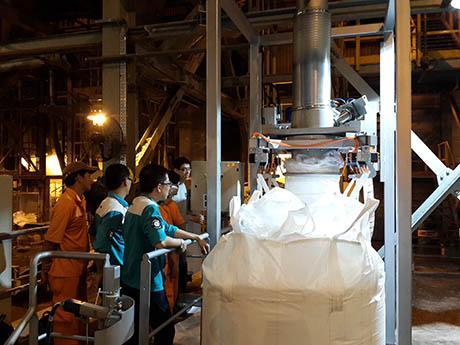
Big bag filling FlowMatic® 04
FlowMatic® 04: automatic filling line for urea and fertilizer in big bags: dosing, packaging and conveying.
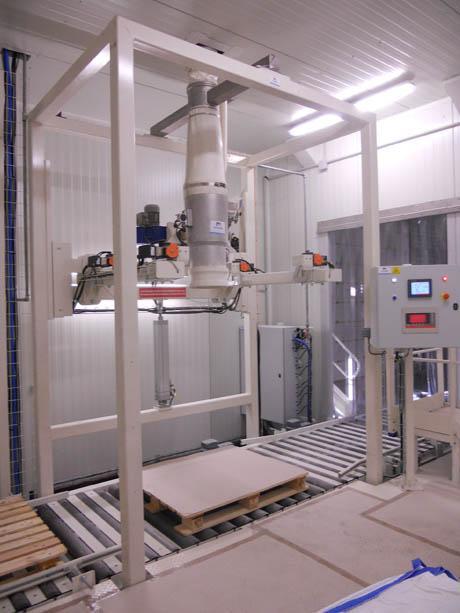
Contained big bag filling system
Cabin for FIBC flowMatic® 04 unloading unit.
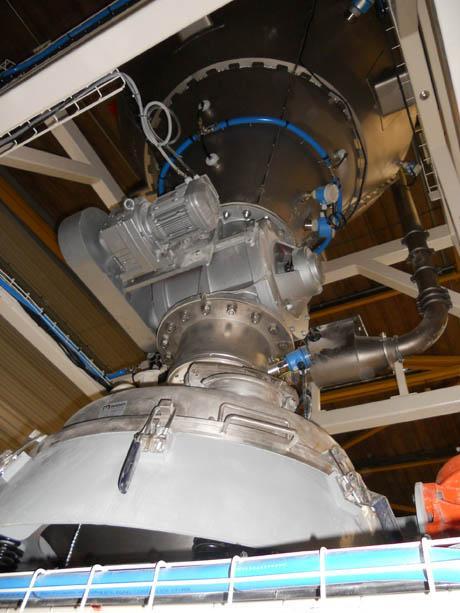
Bulk bag raw material applications feeding hopper
Palamatic Process has developed a high speed big bag packing line with maximum hygiene. The purpose of the process is to condition the bulk material, which is fed from the truck to the buffer hopper, in big bags.
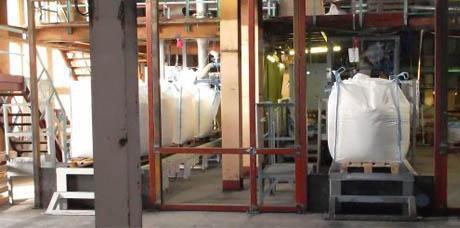
Automatic line processing big bag filling
The big bags of sugar are moved by means of a roller conveyor.
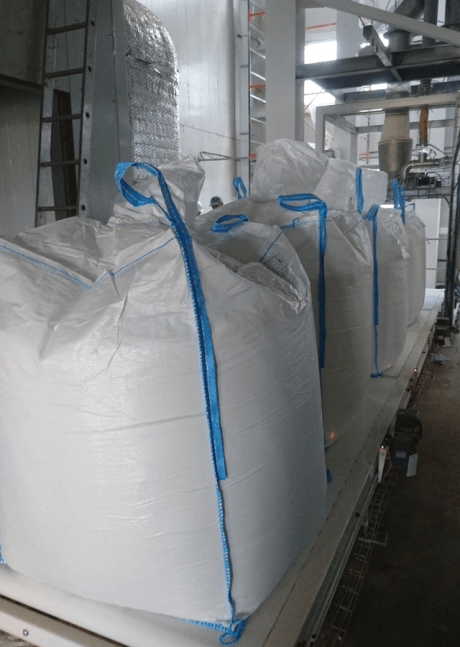
Conveyor on bulk bag charger
The big bag is attached to the structure by means of automatic pneumatic hooks that hold the big bag when it is filled and automatically release the big bag after filling.
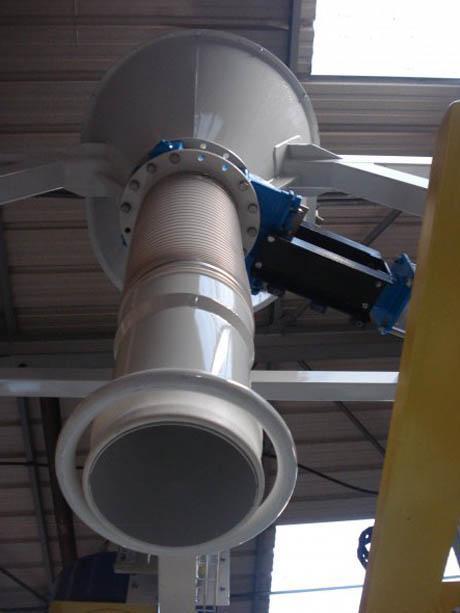
Filling head on FlowMatic® 04
The FlowMatic® 04 big bag filling system integrates all the options necessary for conditioning with a minimum of human intervention.
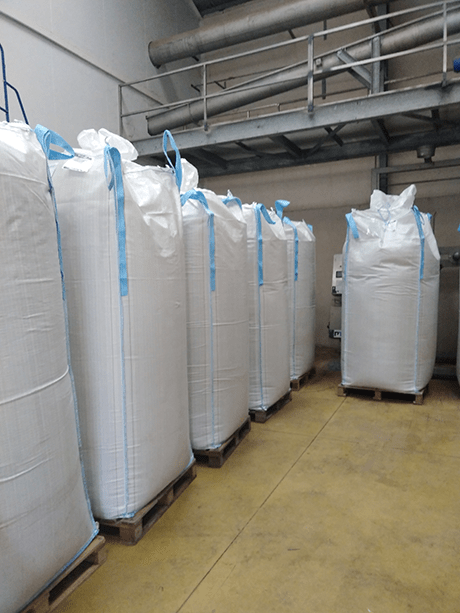
Bulk bag packing line
The automatic removal of the big bag to the storage area is carried out via a roller conveyor.
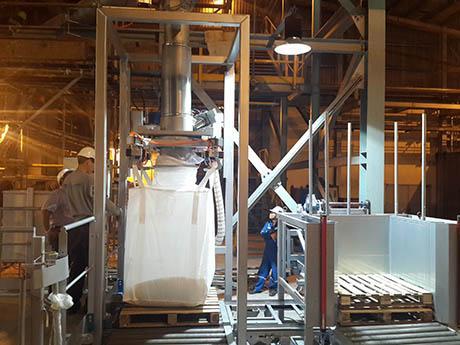
High rate and ergonomic big bag filling station
The FlowMatic® 04 filling machine is designed for continuous use at high flow rates.
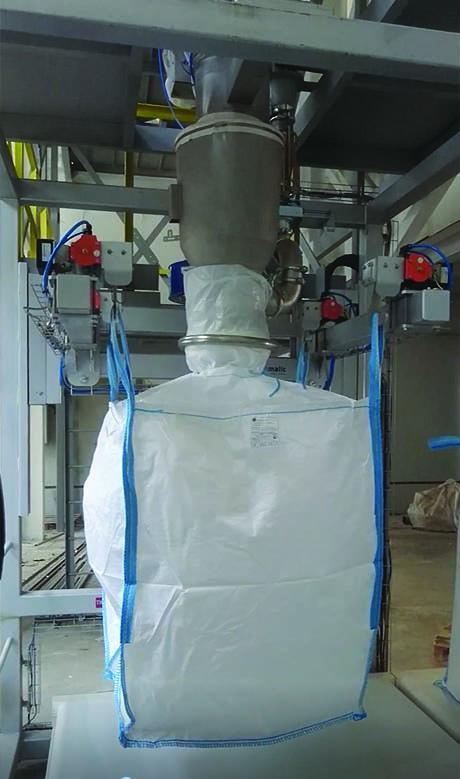
Bulk bag filler
The big bag is pre-inflated to facilitate filling.
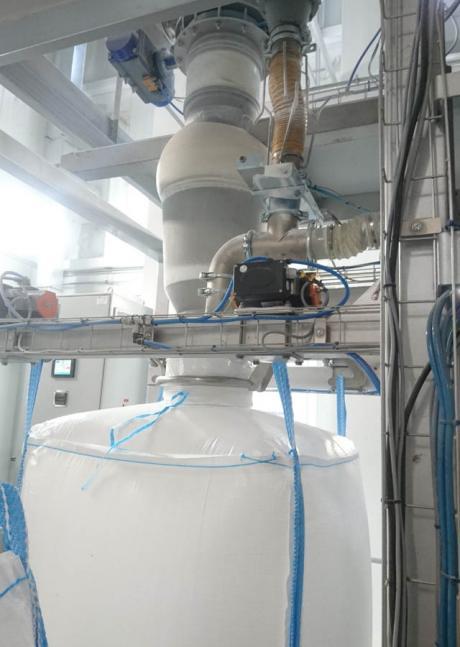
Big bag filler
The big bags of sugar are automatically packed and are weighed gross.
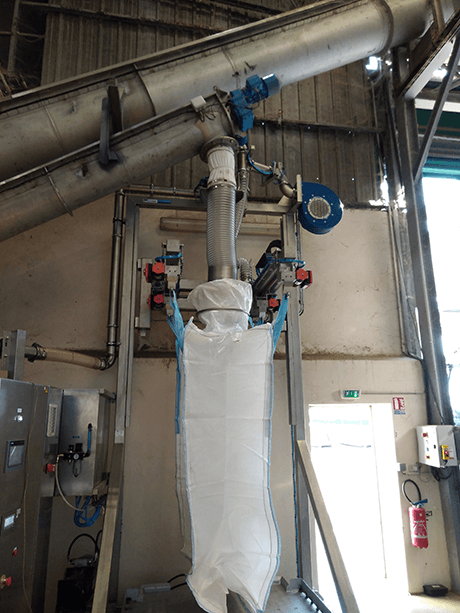
Bulk bag conditioner under screw conveyor
The mechanical conveying screw feeds the big bag filling station.
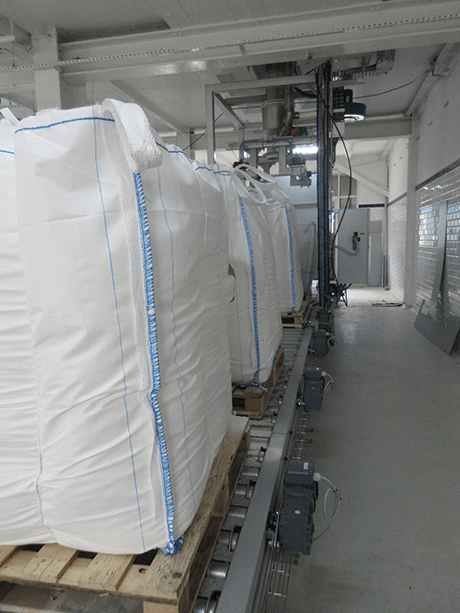
Big bag filling with sugar
Industrial line for powder and big bag handling.
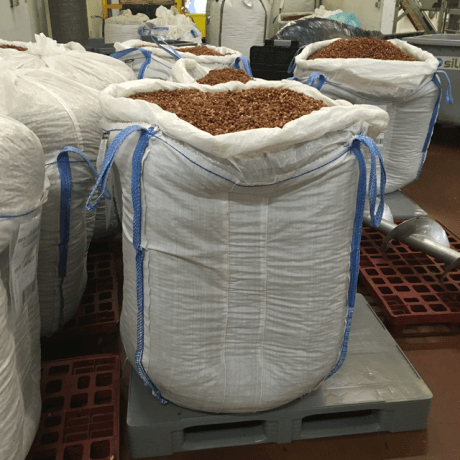
Bulk materials handling
Spice conditioning line in big bags with open mouth.
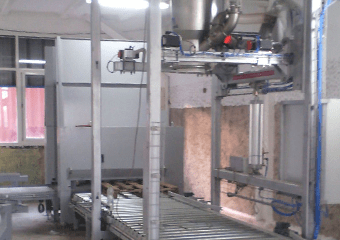
Automated line for big bag filling
The empty pallet supply is automatic.
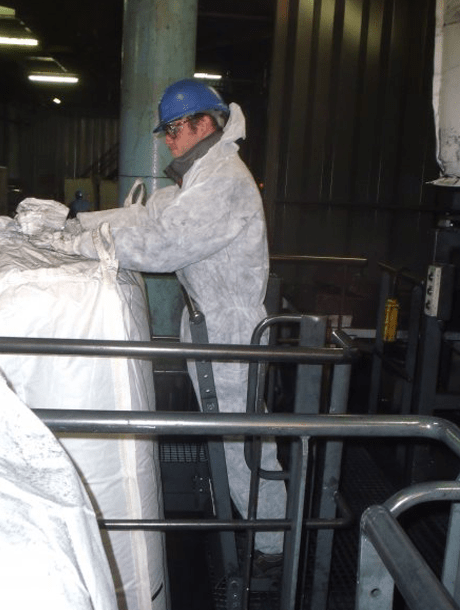
Bulk bag contained filling
The operator platform facilitates access to the upper part of the filling machine to close the big bag filling spout.
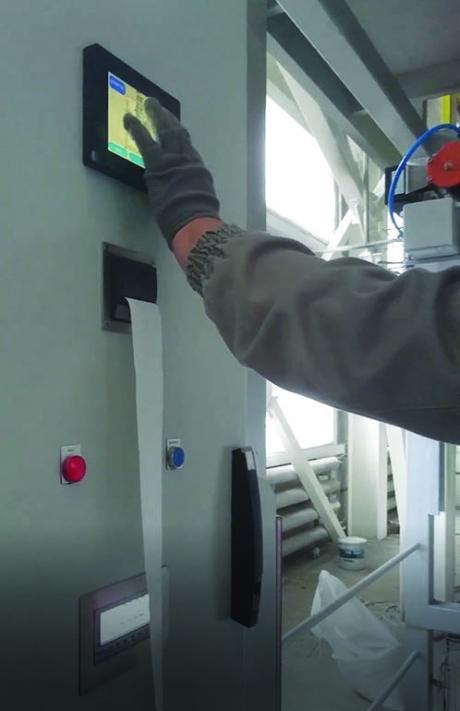
Big bag filling with control cabinet
Automation of the Pal'Touch® line for the packing of sugar in big bags.
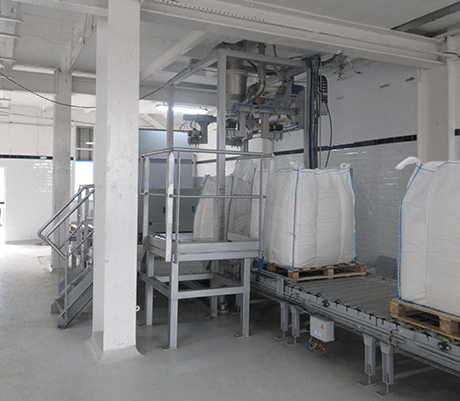
Bulk bag filling line
Industrial production line for filling big bags with sugar.
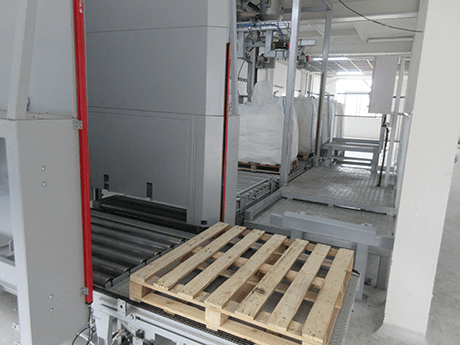
Big bag filling on pallet
The depalletiser is used to automate the big bag conditioning line.
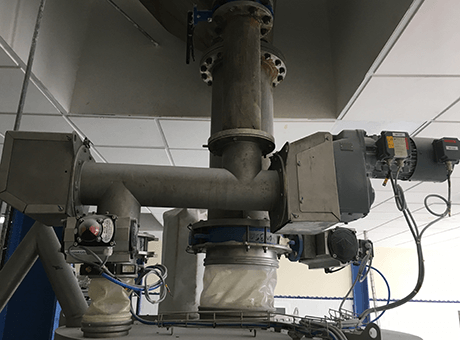
Speed monitoring big bag filling
The filling speed of the powder in the big bag is controlled.
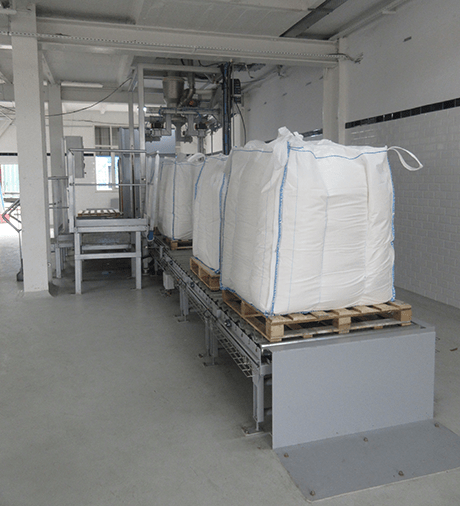
Big bag filling automatic process line
Filling of big bags with seeds through a feeding hopper.
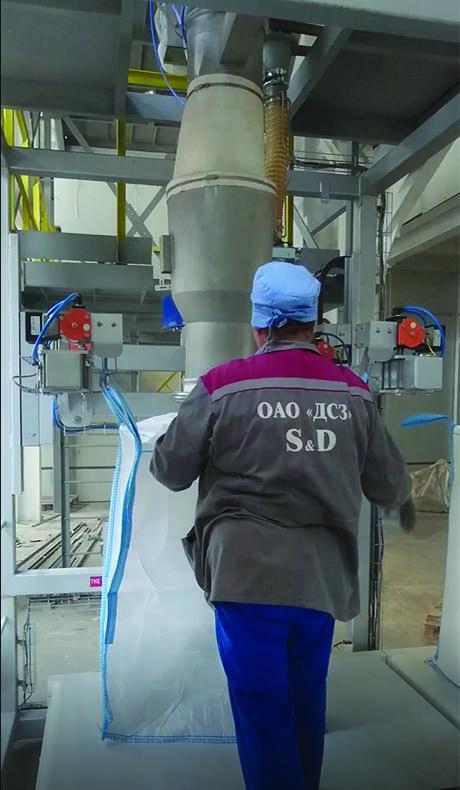
Positioning of the big bag on the station
The big bag is placed on the forks by the operator and the cuff is placed on the filling head of the sugar conditioning station.
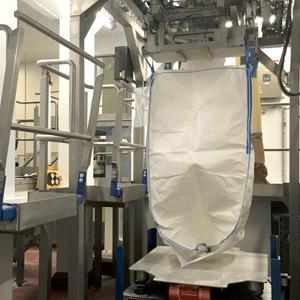
Bagging machine
The removal of the full big bag to the storage area is automatic.
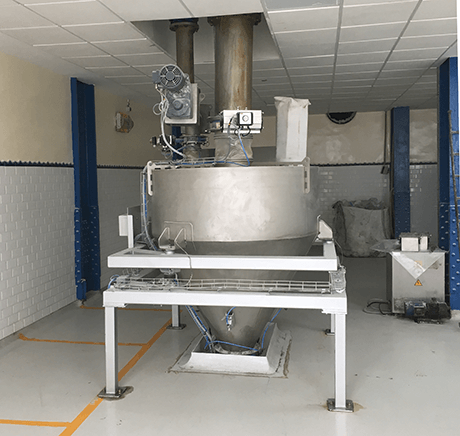
Process hopper
The industrial storage hopper supplies the big bag filling station with iron sulphate.
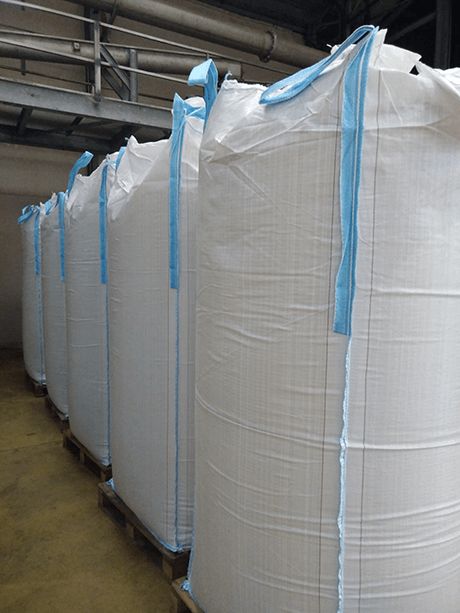
Big bag filling production line
Bulk material storage solutions in Palamatic Process big bag: Pal'Pack®.
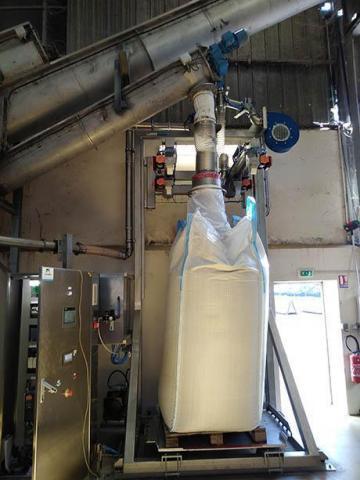
Big bag filling under screw conveyor
Automatic packing line for FlowMatic® 04 big bags for seed conditioning.
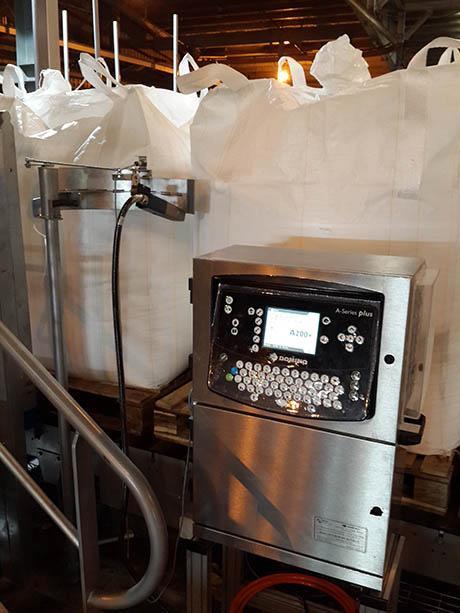
Big bag filling raw materials handling Palamatic Process
Automatic packaging line for FlowMatic® 04 urea big bags: dosing, packaging and conveying of fertilizers.
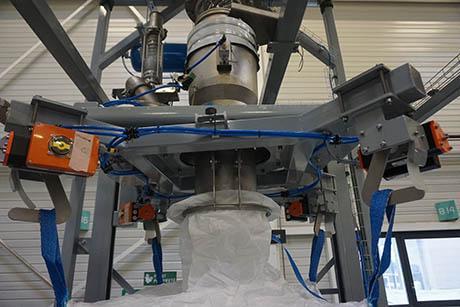
Filling head FlowMatic® 04
Rotating head allows an ergonomic positioning of the big bag on the big bag filling station.
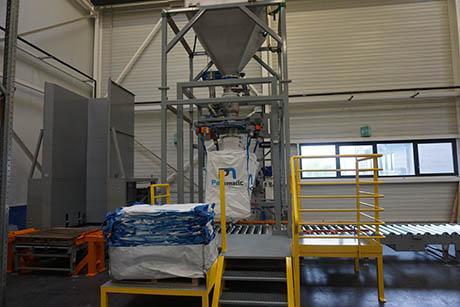
FlowMatic® 04 - Big bag packing
Packing of tobacco dust in big bags.
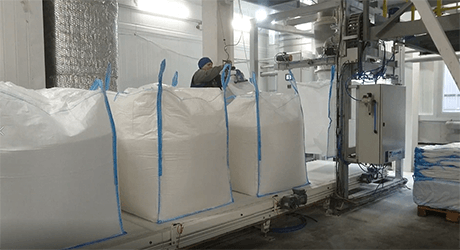
Big bag sewing after filling
Automatized big bag conditioning line with automatic removal of the big bag to the storage area.
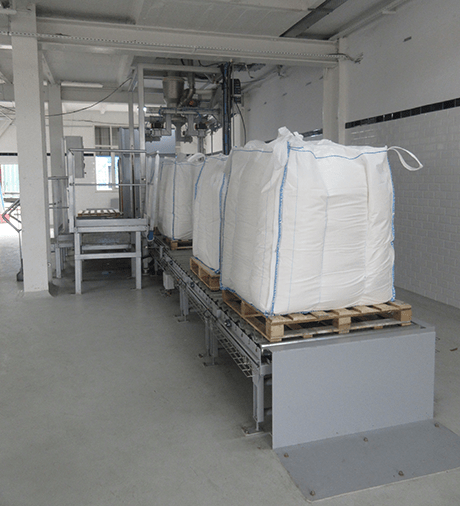
Bulk bag filling
Feeding hopper on big bag conditioner.
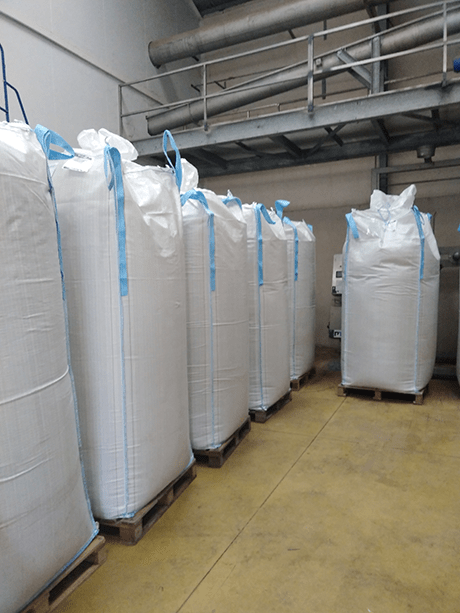
Automatic process line - Bulk bag filling
Dosage and weighing of the big bag conditioner: automation and ergonomics of the workstation.
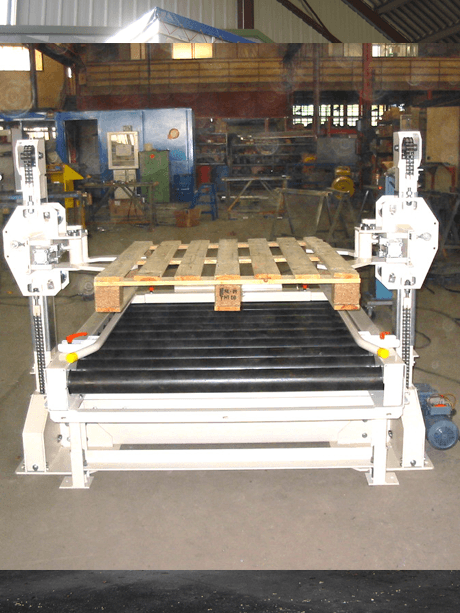
Pallet unstacker
The stacked pallets are stored in the warehouse and then feed one by one the big bag filling station via a motorized conveyor.
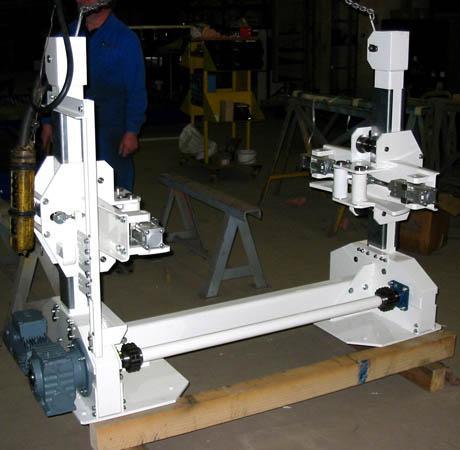
Pallet unstacker
The pallet unstacker is used to automate the big bag filling station.
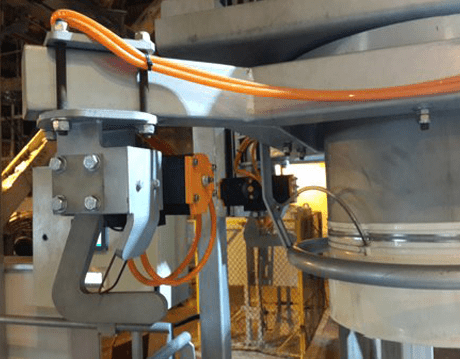
Big bag packing bulk solid
The rotating head on the big bag filling station improves the ergonomics of the workstation.
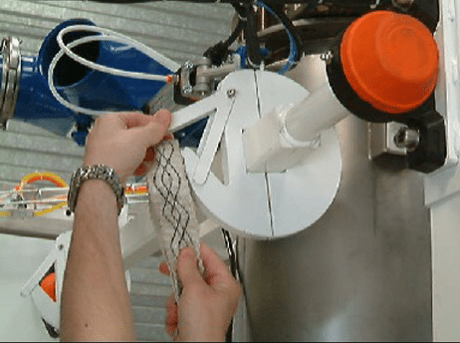
Automatic release
The automatic release of the handles of the big bag facilitates ergonomics and improves the filling rate.
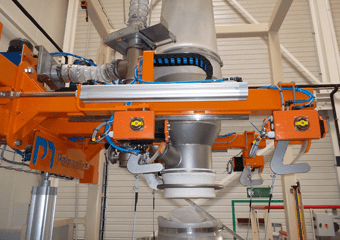
Filling head
Rotating head on big bags filling station on compounding line for the chemical industry.
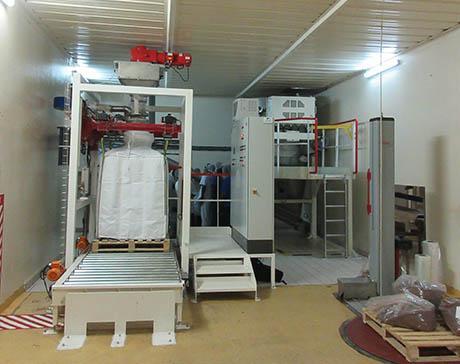
Cocoa powder big bag filling
The extraction of cocoa powder from the buffer hopper for transferring it to an existing big bag packaging station.
The conveying is carried out by an aeromechanical conveyor.
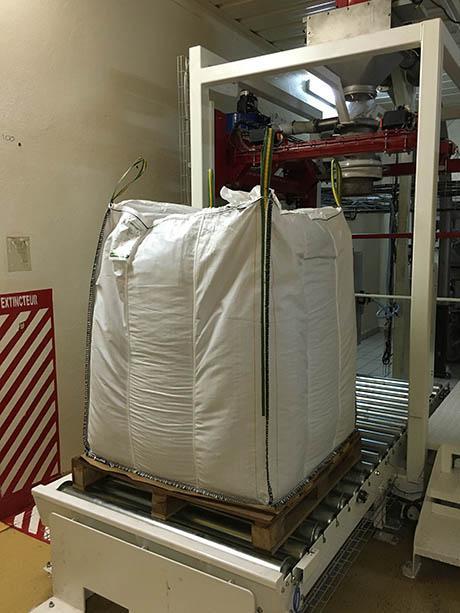
Big bag filling system in the food industry
The cocoa powder is conveyed from the buffer hopper to the big bag conditioner via a mechanical conveyor. The mass flow rate is 2,500 kg/h. for bulk materials with a density of 0.65 kg/l.
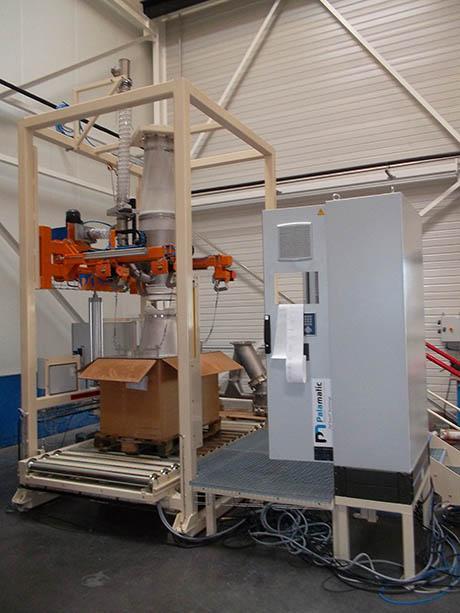
Big bag filling system FlowMatic® 04
Big bag filling station with rotating head to facilitate loading and unloading of the big bag.
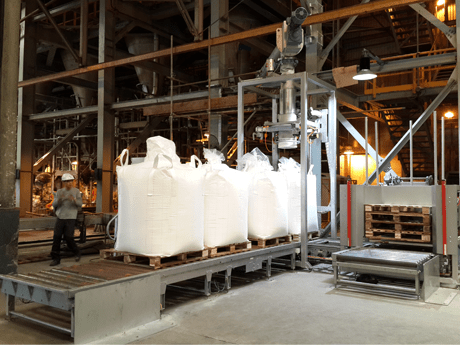
Big bag conveyor - FlowMatic® 04
This installation allows the end product to be extracted from the existing silo through a conveying screw (without an intermediate level to limit Atex risks as much as possible) in order to convey it to the big bag filling station.
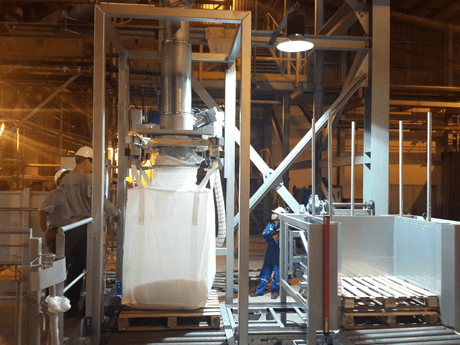
Big bag packing - FlowMatic® 04
To meet the requirements of this customer, Palamatic Process has designed a high flow continuous big bag filling model, called FlowMatic® 04, with throughput rates up to 40 big bags per hour.
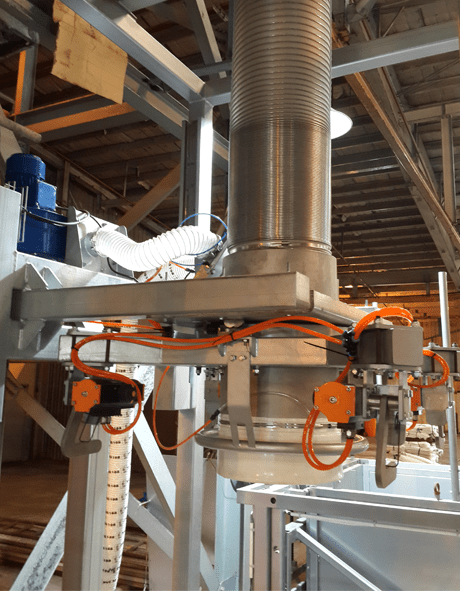
Rotating head
The filling head is designed with a double jacket to ensure volume balancing and is connected to the dust collection system to avoid any dust emission into the atmosphere. Finally, the rotating system of the hooking head makes it easier to attach the handles of the big bag, reducing the operator's operations and maximizing the ergonomics of his station.
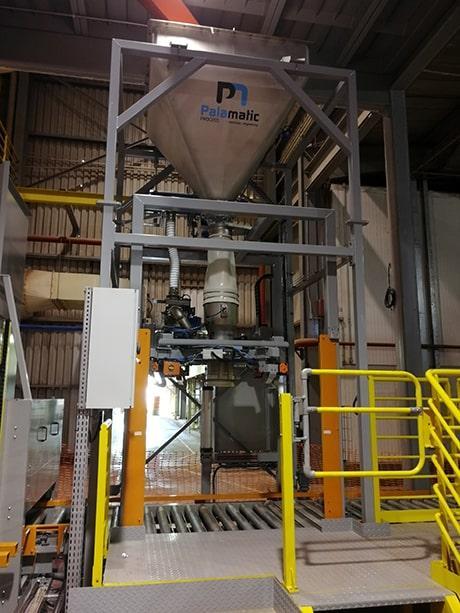
Loading corn seeds
Automatic big bag packing line for corn seeds FlowMatic® 04.
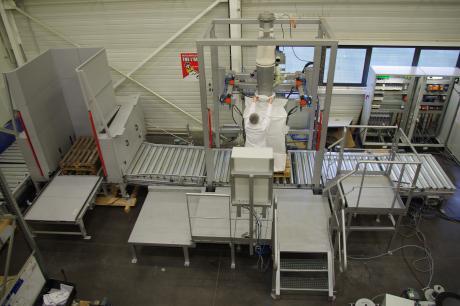
Corn seed packaging line in big bags
The big bag packaging line is equipped with a buffer hopper and a roller conveyor to facilitate the handling of big bags.
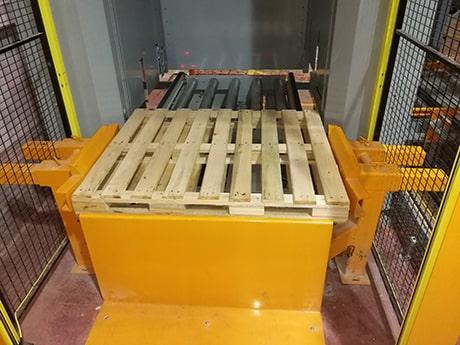
Conveyor for pallets handling
Feeding the conveyor line with empty pallets to distribute the pallets one by one.
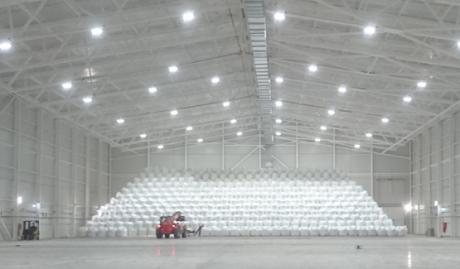
Process line for big bag loading
Big bag charger located at the outlet of a vacuum-pumped pneumatic transfer cyclofilter.
Features
Technical specification
Rate | 20 to 40 big bags/h. |
---|---|
Capacity | 2 tons/big bag |
Manufacturing materials | Painted steel, 304L stainless steel |
Installed power | 8.7 kW |
Compressed air consumption | 6.8 Nm³/h. |
Dust removal rate | 300 m³/h. |
Finishes touches: RAL 9006, micro-blasted, electropolishing
Average power consumption: 1,1 kW
Operating pressure: 6 bar
Input 4-20 mA: 1
Digital input: 14
Digital output: 13
Accuracy of the weighing chain: ± 500 grams
Maximum dimensions of big bags: 1,200 (l) x 1,200 (L) x 2,400 (H) mm
U-shaped forks: allow the removal of the big bag by the loops (optional)
Equipment integrated into the FlowMatic® 04 model:
- Support structure: the structure is manually adjustable in height to fit all types of big bags.
- Automatic removal of bulk bags: four articulated hooks are installed on the reception deck of the bulk bag. The pneumatic cylinder, operated by the automaton, controls the tilting of the hook at the end of the dosing process.
- Inflatable seal: the inflatable seal ensures a tight connection between the filling head and the FIBC during the filling operation.
- Filling head: the filling head is designed in a double casing for volume balancing. The pressure is displaced through the degassing line which can be connected to the dedusting network.
- Tension cylinder: the pneumatic cylinder is located on the deck of the suspension forks. This allows the automated connection of bulk bag handles via height adjustment. This cylinder also allows conformity to varying bulk bag dimensions and aids in the optimal shape of the bulk bag via tensioning during the conditioning phase. The bulk bag is efficiently filled without any risk of air pockets, and can be handled safely without risk of tipping over.
- Pre-inflation fan: the fan ensures the shaping of the FIBC equipped with an internal bag to facilitate material loading. A by-pass valve makes it possible to degas the fines that are captured by the double-cased tube during the conditioning phase.
- Vibrating table: the densification table makes it possible to deaerate difficult products and ensures the optimal filling of big bags. The vibrating table is equipped with two vibrating motors with adjustable intensity
- Pallet unstacker: the unstacker implements, via a motorized roller conveyor, the supply of handling pallets to the packaging station. The pallet size supported by the unstacker is adaptable.
- Roller conveyor: a series of motorized roller conveyors aid in the transfer of empty pallets to the bulk bag packaging station. They are equipped with positioning sensors to ensure a buffer storage of bulk bags at the outlet of the station
Options
Case studies
CASE STUDIES WITH THIS EQUIPMENT
Fertilizers - Urea
Processed powder: urea Fertilizers - Urea Company based in Vietnam, leader in the production of fertilizing products.Chemical
Sugar packing
Processed powder: white sugar - Sugar packing - The FlowMatic© 04 bulk bag filling station allows dust-tight packaging of all types of powders, limits dust emissions and automates the removal of the...Food and Animal Feed
Seed conditioning
Processed powder: treated maize seeds - Seed conditioning - This Multinational, an actor on the world seed market, wants a facility located in Brazil for the automatic packaging of corn seeds in big...Chemical
Loading of ingredients for the production of beverage
Processed materials: citric acid, potassium sorbate, sodium benzoate... - Loading of ingredients for the production of beverage - This installation concerns a new production line in a new building of...Food and Animal Feed
Refined sugar conveying
Processed material: refined sugar - Refined sugar conveying - On-site installation of repackaging equipment for the transfer of sugar stored in shipping containers with an inner liner to a bulk bag...Food and Animal Feed
Automated big bag filling system
Treated powder: spodumene - Big bag filling for lithium battery production - Automated solution with minimal operator intervention.Minerals and building
Production of polyethylene flakes
Processed powder: polyethylene - Production of low-density polyethylene - Company in the petrochemical industry: Installation of 2 big bag packaging lines.Chemical
Railcar unloading
Processed powders: tapioca starch, potato starch, corn starch - Unloading of railcars - Line for powder repackagingFood and Animal Feed
Your quotation in 3 clicks!