Description
Steel & stainless steel IBC containers - Storage of your bulk materials and powders
Storage and conditioning solutons for bulk materials with high hygienic constraints
Steel-Stainless steel IBC container range
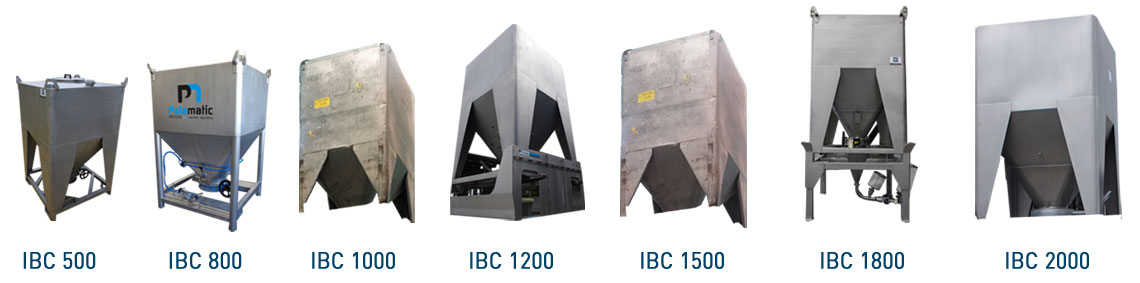
IBC Containers® stainless steel IBC containers are metallic conditioning solutions for the transport, storage and dosage of your powders and bulk materials. Our IBC containers are designed to meet performance, ergonomics and design requirements.
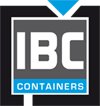
See our website dedicated
to container solutions:
www.ibc-powder-container.com
Palamatic Process designs and manufactures filling and discharge systems for rigid stainless steel containers in optimized containment.
Our IBC container solutions allow to work by lot or batch and offer excellent traceability of your materials. In addition, IBC Containers® centralizes its efforts in designing handy and easy to use materials. The IBC container has 60°slopes and all edges are rounded to avoid retention of the powders. Its supporting structure allows transport by forklift and pallet truck.
This type of powder IBC container is fitted with a butterfly valve that can be operated by a handle or suction cane.
The valve is located inside the IBC container, which protects it from any damage that may be caused by the forks of the forklift truck.
Once the IBC container is in place, a pneumatic cylinder operates the bottom valve and allows the materials to be discharged. The container unloading station can be connected to all conveying systems or to all possible production lines with high containment.
Custom-made IBC containers : IBC Containers that comply with specific constraints
Faced with various industrial constraints, the Palamatic Process engineering office offers customized IBC container solutions to meet the needs of its customers. Their design can be simple or sophisticated depending on the nature of the powders to handle.
IBC containers are at the center of Palamatic Process powder handling system. Designed for rapid operations of filling and discharging with cleaning systems, containers are used to simultaneously implement manufacturing process for optimum production.
Palamatic Process containers are adequate solutions for:
• Transport safety of materials in complete between every stage of production process, without any risk of cross contamination
• The transfer of material from the IBC container to the downstream process equipment without dust emanation
• Easy handling of containers that can be moved by forklifts or hoists.
Applications:
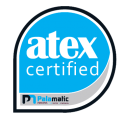
- Buffer storage
- Filling, discharge, weighing
- Continuous and controlled dosing
- Steel or 304 & 316 Stainless steel
- ATEX...
Example of installation:
The container has slopes of 60º and all corners are rounded. The support structure of the container allows transport by forklift truck and pallet truck. The diameter of the top cover is 500 mm in diameter.
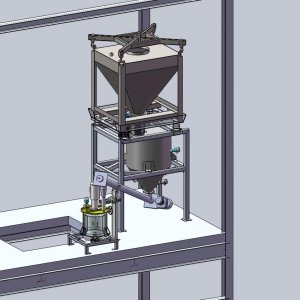
-
Hygiene5
-
Automation5
Equipment advantages
- Stacking on 3 heights
- Hopper with 62° slope to facilitate the flow of materials
- Secure drain valve
- Lifting hooks for overhead handling
- Handling by trolley, stacker or pallet truck
- Handling by the 4 sides
- Corrosion resistance
Media
View our equipment in videos
Container filling station IbcFlow® 01
Industrial container filling head IbcFill® 01
To ensure a dust-tight filling of your containers.
Monitored discharge of the container
The capacity range of our storage containers for bulk materials is from 500 liters to 2,500 liters.
View our equipment in photos
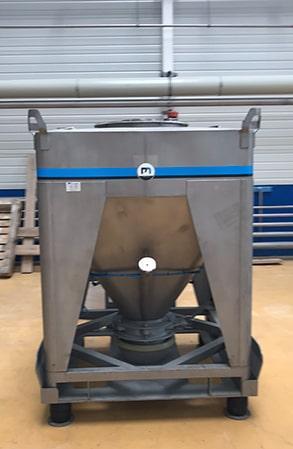
Steel container by Palamatic Process
Industrial steel storage container by Palamatic Process.
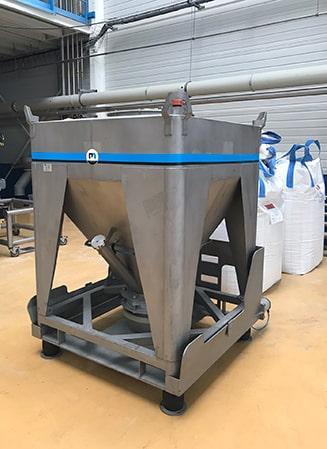
Stainless steel container Palamatic Process
Industrial stainless steel container Palamatic Process suitable for your production lines.
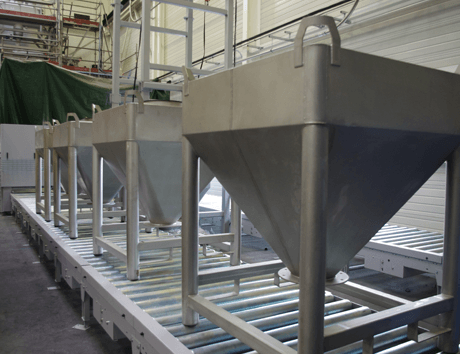
Stainless steel container on roller conveyor
Stainless steel container with hooks for easy lifting.
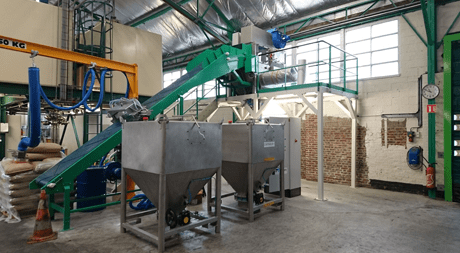
Industrial storage containers on a discharging line
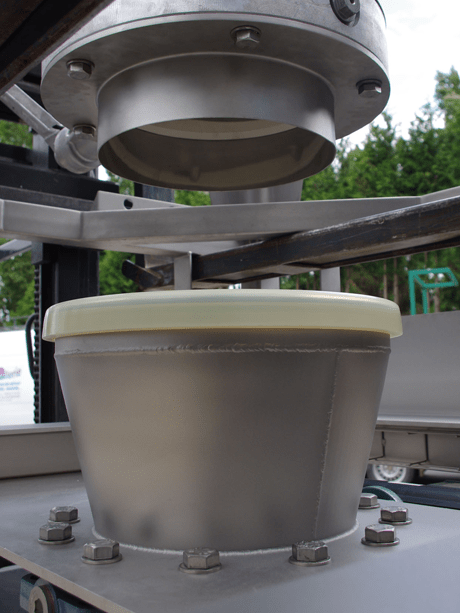
Container docking with sealing gasket
Airtight connection head. A butterfly valve or knife gate valve is also installed to regulate the flow rate.
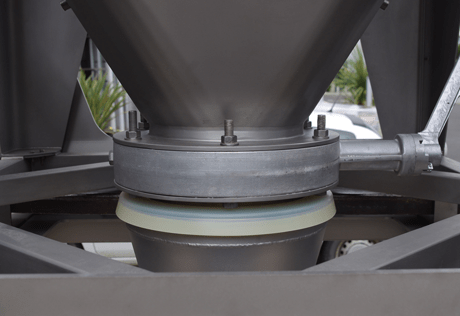
Dust-tight connexion on container
No dust emissions thanks to the airtight connections.
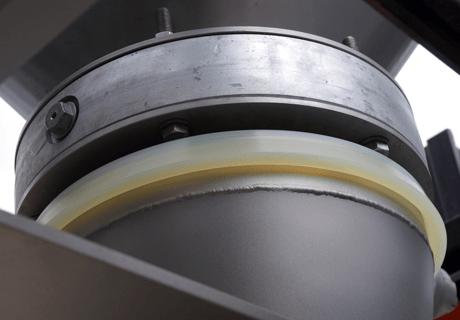
Dust-tight sealing on stainless steel container
No dust emissions thanks to the sealed connections.
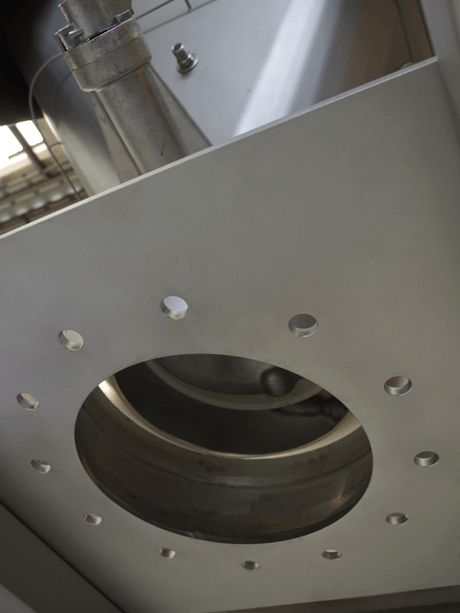
Connexion with dustfree sealing system
Pack and handle powdery products without deterioration and contamination.
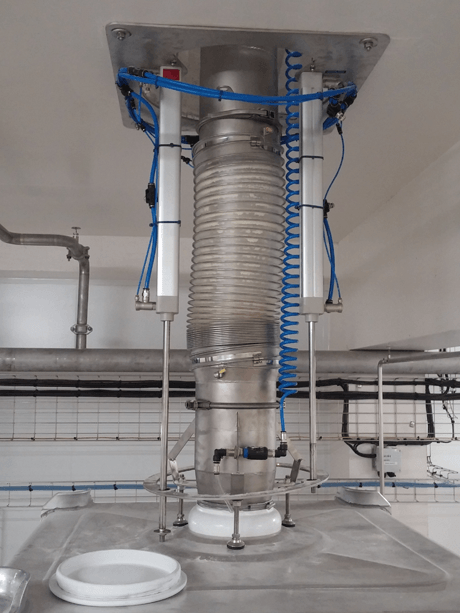
Dust free connexion tube on container
Double envelope container filling head. Sealing of the connection prevents dust and loss of material.
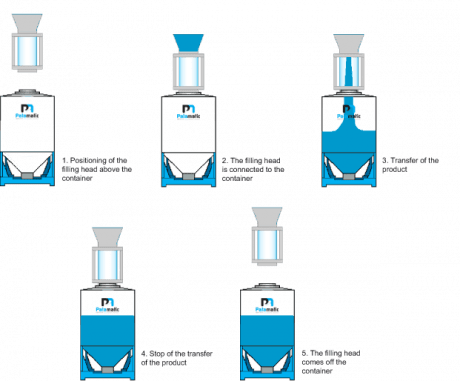
Container filling station
Slope at 62° to facilitate the flow of bulk materials during discharging.
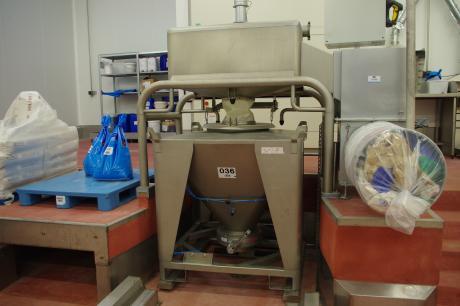
Production line with container filling process
Automatic filling station for stainless steel containers.
The bulk container positioned on a rail is positioned under a dosing unit.
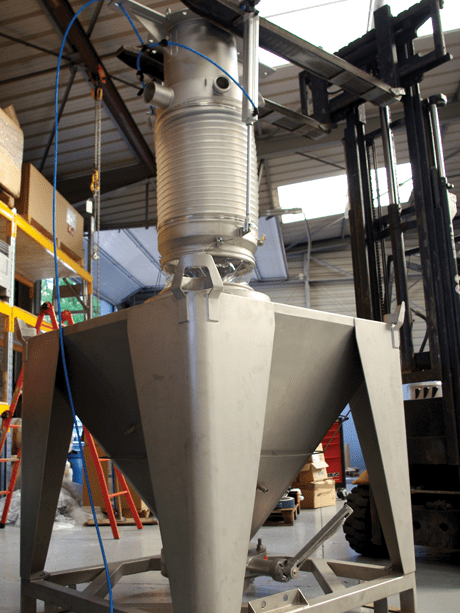
Filling of stainless steel container
For simple packing of bulk and powdery products.
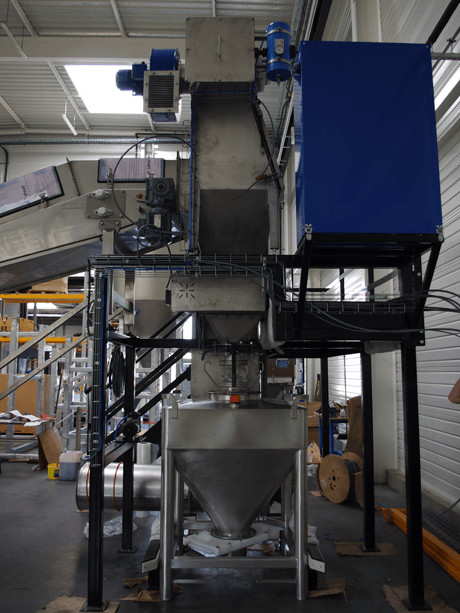
Bulk material processing with industrial containers
The container filling station is suitable for bulk materials that are not sensitive, with low flow rates and facilitate s simple centering of the filling head on the container.
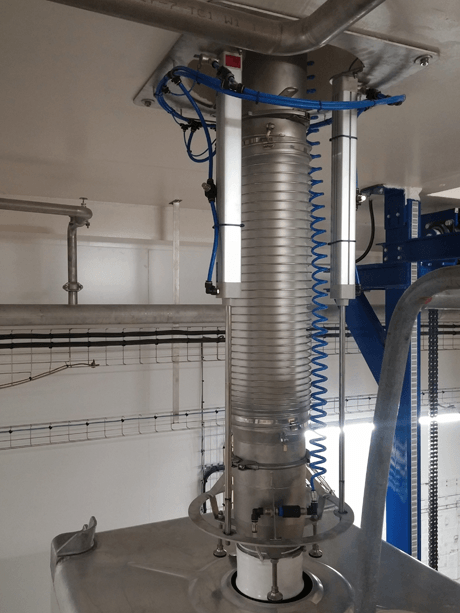
Telescopic tube with FDA metal spirals
Double envelope container filling head. The sealing of the connection prevents dust emissions and loss of materials.
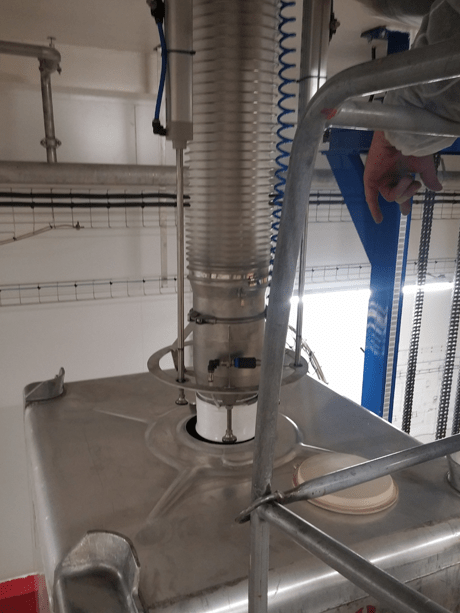
Container dust-tight filling with flexible connector
The container filling station is provided with a flexible fitting to avoid weighing interference.
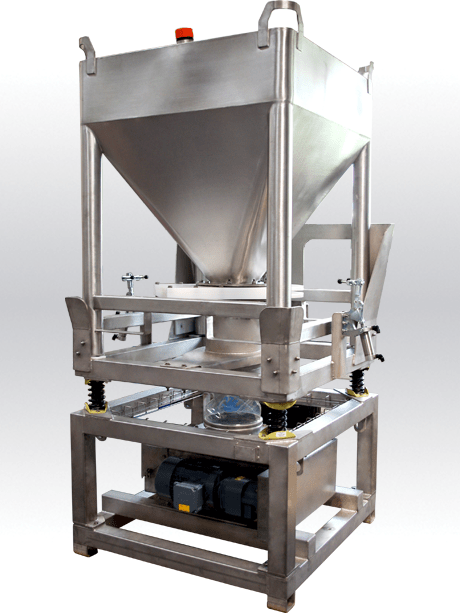
Container discharging station IBC FLOW 01
For a controlled emptying of your bulk materials. The station ensures containment and flow optimization during container emptying.
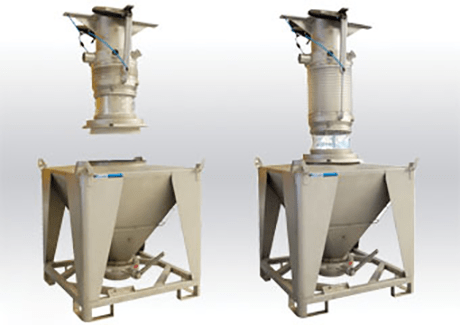
Automatic or manual container filling
Manual or automatic container filling stations provide precise dosing and total hygiene.
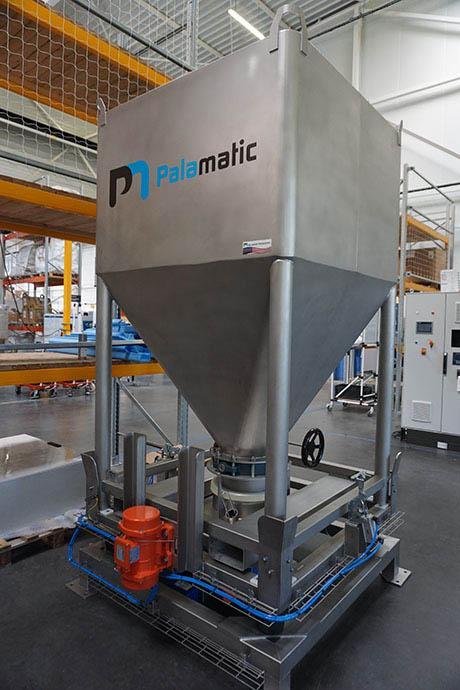
Storage in containers of veterinary powders
For the packing and storage of bulk materials with high hygienic requirements.
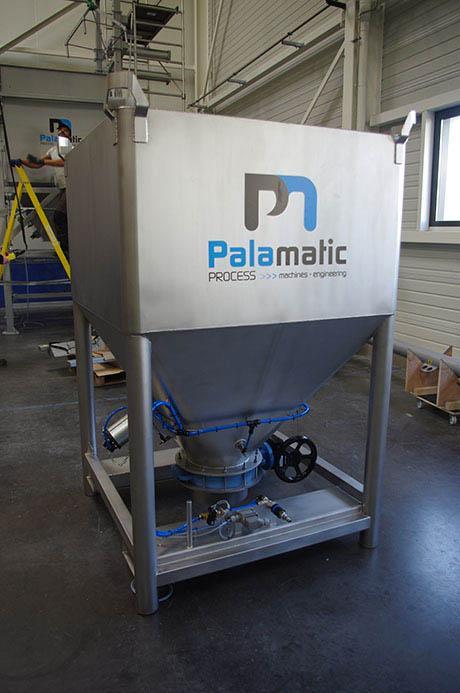
Industrial container for storage of dyes and pigments
Automatic dosing and filling of pigments for a plaster manufacturer.
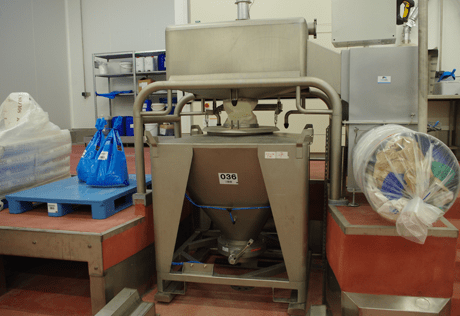
Stainless steel container loading station
500, 1000, 1500, 1500, 1800, 2000 and 2500 liters as standard
Made of steel, stainless steel 304 and stainless steel 316 L
Custom made models available
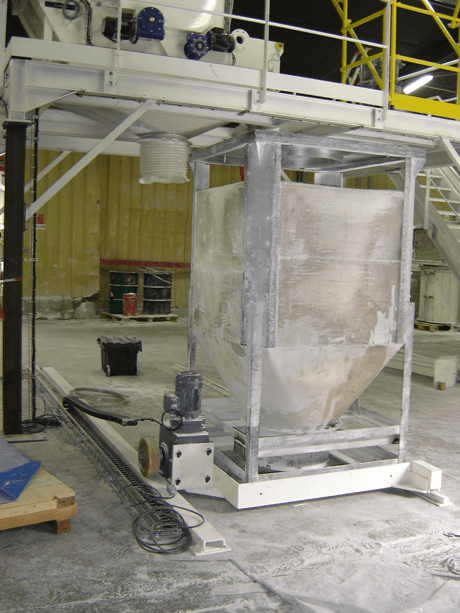
Dust-tight filling of industrial containers
The IBC Containers® filling head allows you to connect a hopper to a container in a completely sealed manner to carry out a gravity transport of your bulk materials.
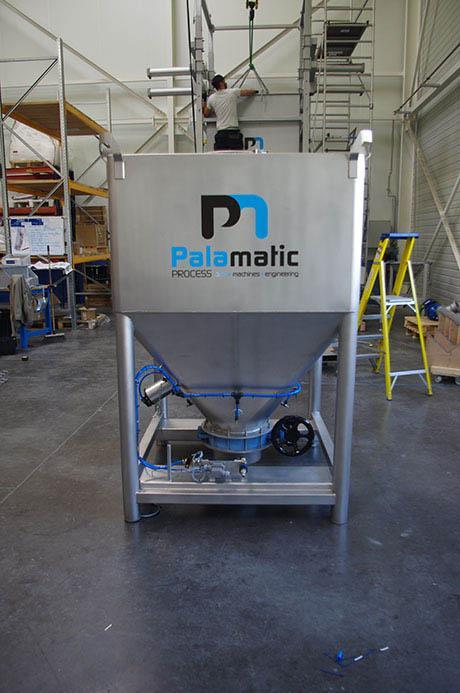
Stainless steel container for calcium carbonate
Packing of calcium carbonate for the manufacture of chalk.
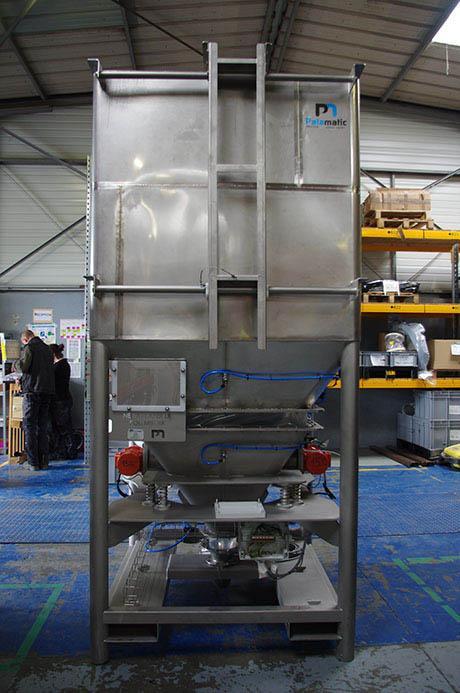
Spices storage in industrial container
Packing of food spices (curry and paprika). The station collects spices from the industrial mixer. The spices are then sieved before packing in the steel-stainless container.

Connexion tube for container loading
The container filling station connects to the storage container via the telescopic connection sleeve.
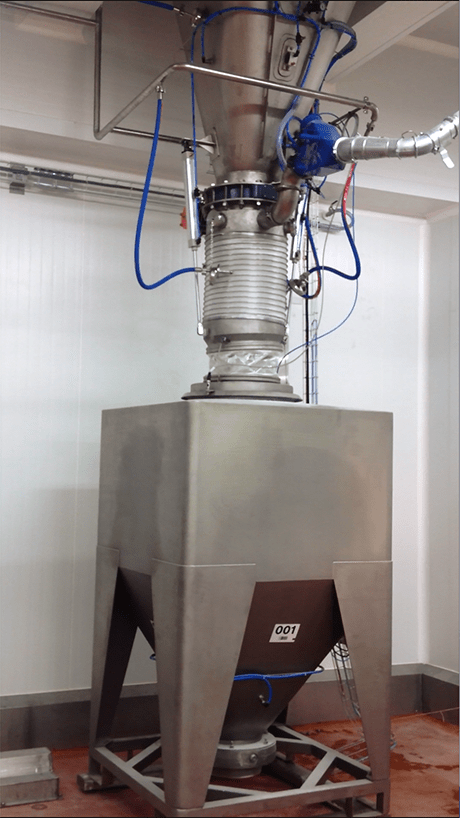
Dust-tight telescopic filling tube
The presence of a socket joint ensures containment and provides high flow rates.
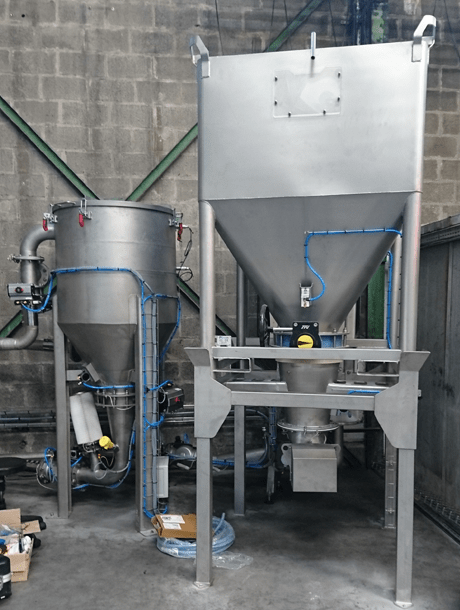
Container discharging station on pneumatic conveying line
Equipment:
- Dense phase vacuum pneumatic conveying with detached filter
- Dense phase vacuum pneumatic conveying VFlow® 05
- Steel / Stainless steel container
- Container unloading station IbcFlow® 01
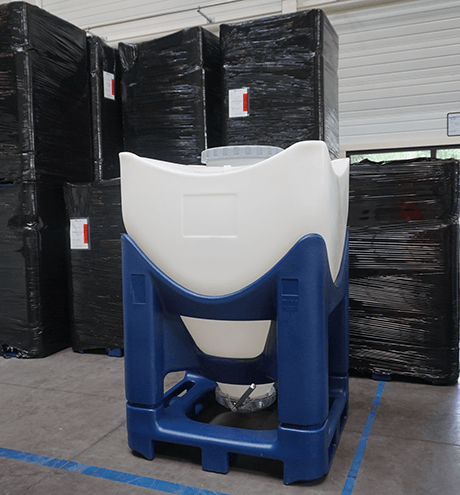
Container filling station
The operator lifts the bag using the manipulator. The bag is then unloaded into the discharge station. To complete the process, the powder is hygienically poured into the container.
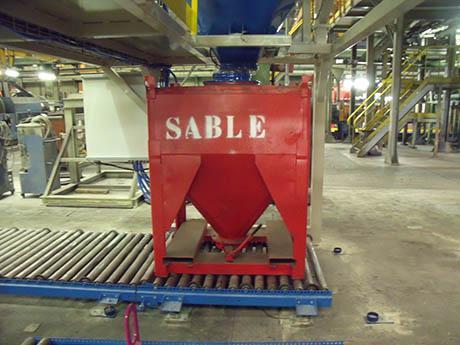
Steel manufacturing container
Storage containers on roller conveyor.
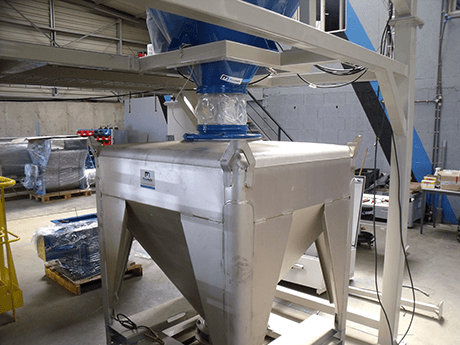
Industrial container for bulk materials storgae
The industrial container is fed with powders through a flexible connector.
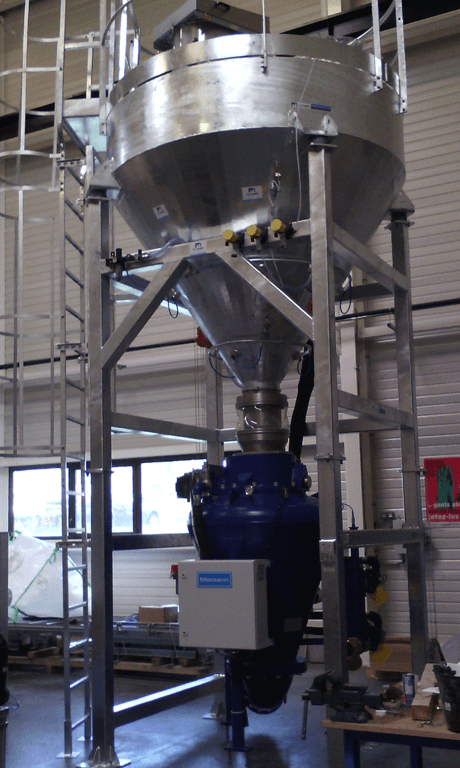
Buffer hopper manufactured in stainless steel
This industrial container is supplied with a butterfly valve that can be operated by a handle.
The valve is located inside the container, which protects it from any damage that may be caused by the forks of the forklift truck.
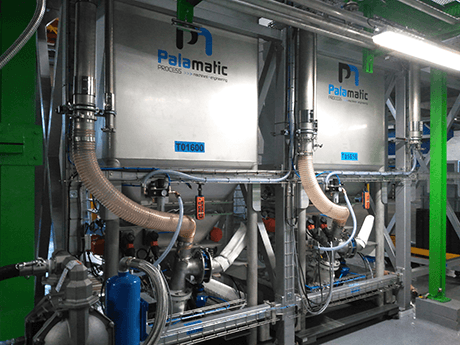
Container on a liquid formulation line
These industrial stainless steel containers are part of an industrial production line including:
- 3 big bag discharging stations for 7 types of materials
- 3 stainless steel container for repacking and unloading stations
- 2 vacuum pneumatic conveying lines feeding 2 reactors
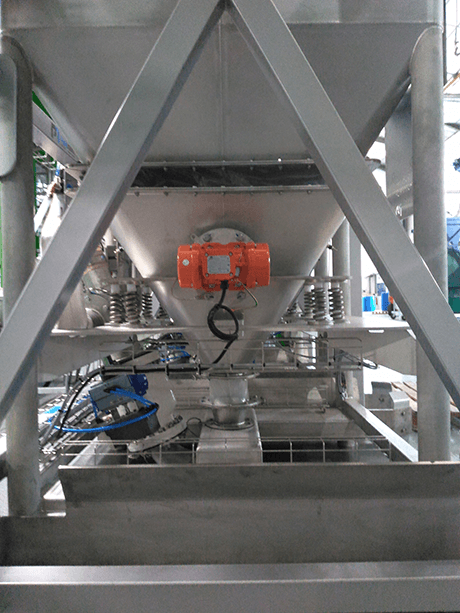
Weighing system on container
The stainless steel industrial container is provided with 4 bin aerators on the conical part and an anti bridging device with spring and 2 motovibrators on the conical part.
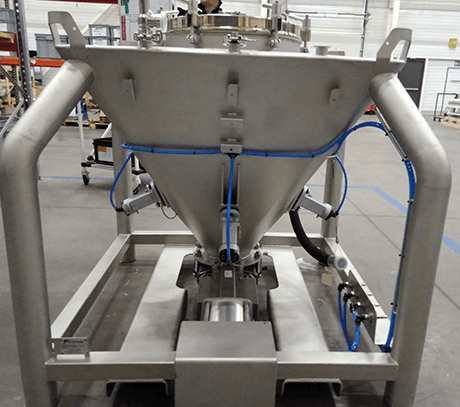
Wet powder stored in industrial container
The wet powder is packaged in stainless steel containers at the dryer outlet.
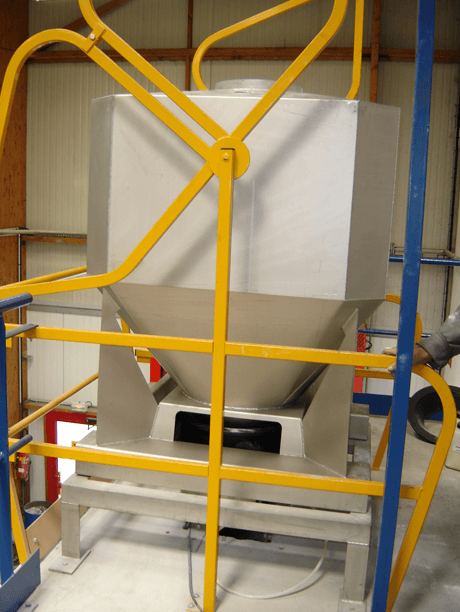
Discharge station for industrial containers
This equipment is intended for handling raw ingredients and bulk materials whose capacity must be adapted to your needs.
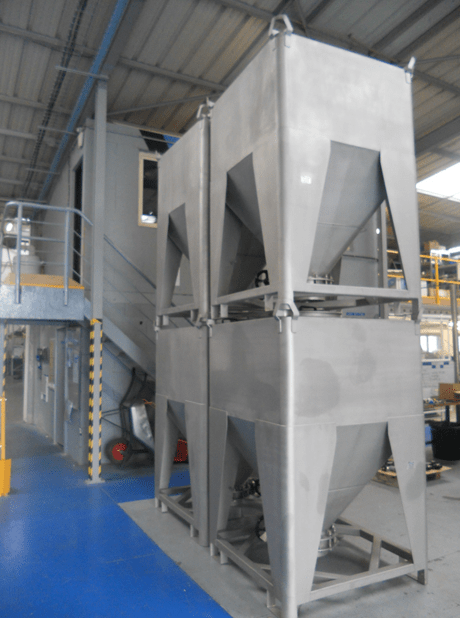
Sugar storage in containers
- Slopes of 60º and all corners rounded.
- Container support structure with base for forklift and pallet truck handling
- 500 mm diameter cover
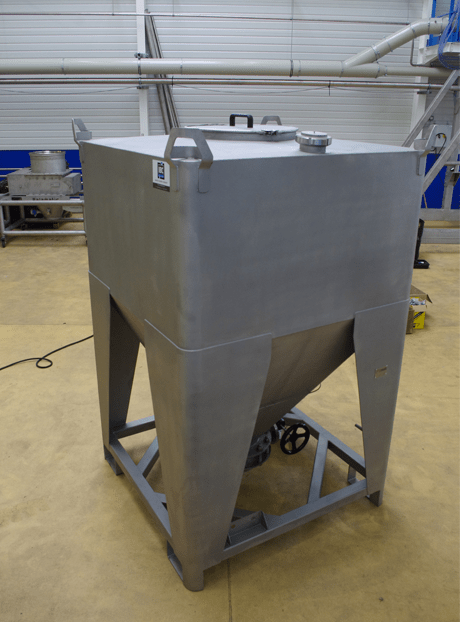
Storage of sugar in industrial containers
Once the filling nozzle has been lowered onto the container and connected tightly (inflated seal), the vacuum pump is started, connected to the double jacket of the filling head, to remove the untreated air. The container discharge valve remains closed.
Features
Technical specification
Dimensions :
Models (butterfly or slide valve) | IBC 500 | IBC 800 | IBC 1000 | IBC 1200 | IBC 1500 | IBC 2000 |
---|---|---|---|---|---|---|
Water volume in liters* | 500 | 800 | 1 000 | 1 200 | 1 500 | 2 000 |
Base dimensions in mm | 1204x1204 | 1204x1204 | 1204x1204 | 1204x1204 | 1204x1204 | 1204x1204 |
Overall height in mm | 1374 | 1567 | 1717 | 1867 | 2067 | 2417 |
Outlet Ø in mm | 250 | 250 | 250 | 250 | 300 | 300 |
*10 to 20% decrease for the material volume
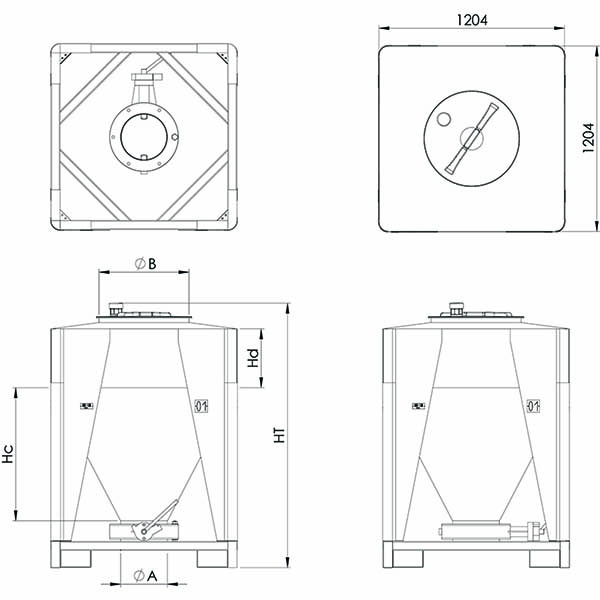
Water volume | Effective volume* | Weight when empty (kg) | ØA | ØB | Hd | HT | Hc | Slope in ° | |
---|---|---|---|---|---|---|---|---|---|
IBC 500 | 573 | 474 | 215.5 | 300 | 575 | 0 | 1374 | 864 | 62 |
IBC 800 | 908 | 778 | 238 | 300 | 575 | 232 | 1567 | 864 | 62 |
IBC 1000 | 981 | 850 | 250 | 300 | 575 | 382 | 1717 | 864 | 62 |
IBC 1200 | 1343 | 1211.50 | 264 | 300 | 575 | 532 | 1867 | 864 | 62 |
IBC 1500 | 1632 | 1501 | 283 | 300 | 575 | 732 | 2067 | 864 | 62 |
IBC 1800 | 1909 | 1803 | 306.5 | 300 | 575 | 980 | 2314 | 864 | 62 |
IBC 2000 | 2138 | 2007 | 316.5 | 300 | 575 | 1082 | 2417 | 864 | 62 |
Options
Case studies
CASE STUDIES WITH THIS EQUIPMENT
Process of plasterboard production
Processed powder: plaster - Process of plasterboard production - French company producing and selling plaster, products derived from plaster and products based on expanded polystyrene.Minerals and building
Rubber calendering line
Processed powders: 2 references of carbon black (micro pearl) - Rubber calendering line - The facility includes 2 container discharge systems that supply 2 mixing lines with powdered carbon black.Chemical
Masterbatch and additives
Processed powders: cobalt, calcium carbonate CaCo3, titanium dioxide TIO2 - Masterbatch and additives - Discharge of raw materials while maintaining a healthy atmosphere without pollution and without...Chemical
Washing powder
Processed powder: laundry powder - Washing powder - This company was looking for a storage solution for humidified laundry powder with an apparent density of 1.3.Chemical
Pharmaceutical loading
Processed powder: Sorbitol - Pharmaceutical loading - Manufacturing of basic pharmaceutical products, medicinesFine chemical
Cake mix
Processed powders: modified starch, sodium bicarbonate, fat powder, whipping base, gelatin, milled sugar - Cake mix - Company based in Saudi Arabia that manufactures and distributes dry food materials...Food and Animal Feed
Animal nutrition food supplements
Processed powders: silica, clay, calcium carbonate, lithothamnium - Animal nutrition food supplements - This customer is a producer of specific mixtures of botanical extracts. In order to ensure its...Food and Animal Feed
Premix manufacturing
Processed powders: silica, wheat, carbonate - Premix manufacturing - The installation consists of a new mixing line for the production of natural additives for animal nutrition.Food and Animal Feed
Handling of veterinary bulk solids
Processed bulk solids: veterinary powders - Loading of veterinary powders - Company specialized in animal nutrition and health: workshop for the preparation and mixing of bulk materialFood and Animal Feed
Loading of ingredients for the production of beverage
Processed materials: citric acid, potassium sorbate, sodium benzoate... - Loading of ingredients for the production of beverage - This installation concerns a new production line in a new building of...Food and Animal Feed
Preparation of spice mixtures
Processed products: spices - Preparation of spice mixtures - The objective is a spice blending line with cleanability of the equipment and recipe flexibility.Food and Animal Feed
Confined deconditioning, dosing and transfer of powders
Processed powders: Minerals and additives (such as titanium dioxide) for the manufacture of paints - Emptying of big bags into mobile IBCs with dosing and transfer of the product to a mixer downstream...Chemical
Yogurt and cheese production line
Processed products: milk powder - Yoghurt and cheese production line - The function of the equipment is to add milk powder mechanically in tanks.Food and Animal Feed