Palamatic Process containment systems integrate filtration and containment technologies, ensuring protection against dust emissions and contamination risks. They are equipped with real-time monitoring devices, enabling rapid detection and correction of any anomalies or potential leaks.
Palamatic Process offers ranges for the containment of CRM (Critical Raw Materials) and toxic powders, applicable to a wide range of industries, including the battery industry. This industrial equipment is designed to ensure safe and efficient handling of critical and toxic materials, meeting the most stringent safety and regulatory compliance requirements.
1. Presentation of the confined systems range
Confined bulk bag emptying stations
This equipment enables bulk bags to be emptied in complete safety, without releasing powders into the environment. They are designed to guarantee maximum tightness when connecting, emptying and disconnecting bulk bags, and can be fitted with filtration systems for additional protection.
Pneumatic transfer systems
These systems enable powders to be transferred from one point to another safely and efficiently, using compressed air to move the products through leak-proof hoses. They reduce the risk of powder dispersion and cross-contamination, and minimize manual handling.
Confined mixers
These systems mix powders homogeneously and precisely, while ensuring total product containment. They are designed to reduce material losses and dust emissions, and can be adapted to the specific needs of each application.
Dosing and weighing units
These systems enable precise dosing and weighing of powders. These modules complete lines that can be integrated with other equipment in the Palamatic Process range to create appropriate solutions for powder processing.
Automated filling systems
This equipment enables containers (bags, drums, bulk bags, etc.) to be filled automatically and safely. They reduce the risk of human error, cross-contamination and the dispersion of powders in the environment.
Palamatic Process' confined systems offer comprehensive solutions tailored to the specific needs of industries handling hazardous or sensitive substances. These systems help to improve the safety, quality and efficiency of manufacturing processes.
2. The Sacktip® SE contained sack manual discharging station
The Sacktip® SE contained sack manual discharging station from Palamatic Process is an innovative solution designed for the safe handling of toxic or hazardous products.
Key features of the Sacktip® SE confined manual bag emptying station
Total containment
The sealed door with glove box protects operators when opening and emptying bags. Bags are introduced from the side through a sealed door. Once the bag has been emptied, it is evacuated from inside the glove box to a bag compactor or waste garbage can. In this way, the bag never leaves the system.
Integrated dust removal
All cabins are equipped with integrated dust collection outlets or filters to maintain a healthy working atmosphere.
Optimized ergonomics
The design allows easy bag handling with minimum operator effort.
Sacktip® SE technical specifications
-
Throughput: 2 to 6 bags per minute
-
Materials: Available in painted steel, 304L stainless steel or 316L stainless steel
-
Door options: Steel, stainless steel, Plexiglas or tempered laminated glass
-
Gloves : Latex, natural rubber, polyurethane, Hypalon or Butyl
-
Sealing: EPDM, NBR, natural rubber or silicone gaskets
Key benefits
Enhanced safety
Hazardous substances are handled in a closed environment
Improved hygiene
Mirror-polished finish for improved flow and hygiene
Flexibility
Available in 4 standard models to suit different bag sizes
Customization
Configurable to specific customer requirements
Industrial applications
The Sacktip® SE is ideal for industries handling toxic or hazardous materials.
Chemistry
Chemistry is a science that studies the composition, structure, properties and reactions of substances.
Petrochemistry transforms petroleum into chemical derivatives used in various sectors.
Fine chemistry is the production of specialized chemical substances used in the pharmaceutical, food and cosmetics industries.
Green chemistry in the development of chemical elements and processes that minimize the use and generation of hazardous substances.
Nuclear power
The nuclear sector concerns the use of nuclear energy in a variety of applications.
Electricity generation through the use of nuclear reactors.
Nuclear medicine and the radioisotopes used to diagnose and treat disease.
Scientific research into the structure of matter and nuclear reactions.
Food processing (for certain additives)
The food industry transforms agricultural raw materials into foodstuffs.
Preservatives, which extend the shelf life of foodstuffs by inhibiting the growth of micro-organisms.
Colorants, which improve the appearance of food.
Emulsifiers to mix substances that do not mix naturally, such as oil and water.
The pharmaceutical industry
The pharmaceutical industry is responsible for the discovery, development, production and marketing of medicines.
In research and development, through the discovery of new molecules and drug development.
In the production and manufacture of medicines to strict quality standards.
In the distribution and marketing of medicines to pharmacies and hospitals.
These fields are interconnected and often dependent on each other for the development of new technologies and products.
The Sacktip® SE emptying station by Palamatic Process offers a complete solution for the safe manual unpacking of hazardous substances, combining safety, ergonomics and efficiency to meet the stringent requirements of sensitive industries.
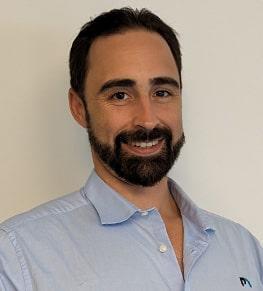
Do you have a project?
I am available to advise you and help you with your project.
Tarik, expert in powder containment
3. The BaggerCake® process
Palamatic Process's automated process for packaging filter cake in bulk bags represents an innovative solution for the battery industry in particular. This technology, called BaggerCake®, offers an efficient and safe approach to filter cake packaging.
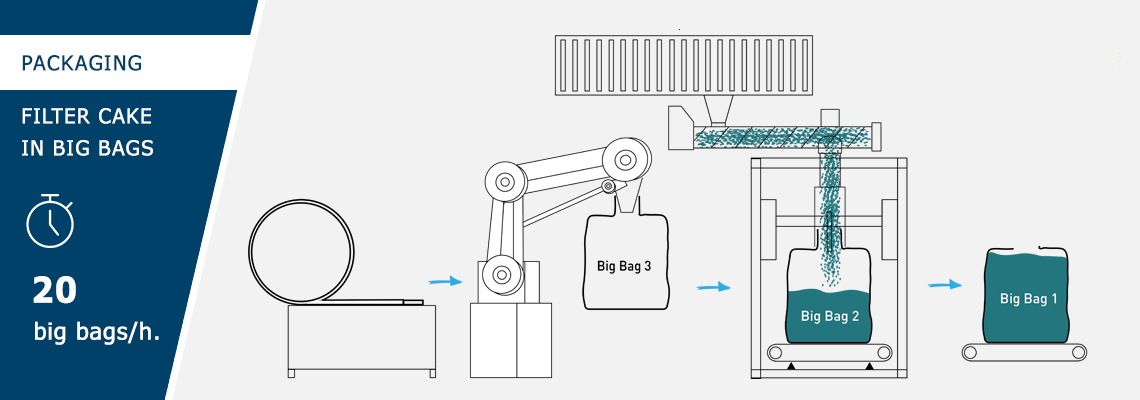
Automated packaging process for filter cake in bulk bags
How the BaggerCake® system works
Product transfer
A screw transfers the filter cake to a bulk bag filler, which can be semi- or fully automatic.
Bulk bag filling
The filling machine is equipped with advanced features to ensure precise, efficient filling.
Automation
The system is designed for automated operation, reducing the need for human intervention and increasing productivity.
BaggerCake® benefits
Optimized safety
The automated process minimizes operator exposure to potentially hazardous materials, a crucial aspect in the battery industry.
Increased efficiency
Automation enables fast, accurate packaging, boosting overall line productivity.
Flexibility
The system can be adapted to meet the specific needs of different industries and types of production.
Product quality
Precise filling and careful handling of the filter cake contribute to maintaining the quality of the final product.
Industrial applications
Although initially designed for the battery industry, the BaggerCake® system can be adapted to a variety of industrial applications requiring the packaging of filter cake or similar elements in bulk bags. This versatility makes it an attractive solution for many industrial sectors.
Palamatic Process's automated packaging of filter cake in bulk bags represents a significant advance in industrial automation. By combining safety, efficiency and flexibility, the BaggerCake® system offers a complete solution for companies seeking to improve their packaging operations, while ensuring the safety of their employees and the quality of their production.
4. The PCaMatic® process line
The PCaMatic® process line from Palamatic Process represents a breakthrough in the automation of PCAM (Precursor Cathode Active Material) preparation for the battery industry. This technology is designed to optimize the preparation of PCAM prior to its transformation into CAM (Cathode Active Material) in furnaces, offering a safe and efficient solution for the transfer and blending of lithium, nickel, manganese and cobalt hydroxide powders.
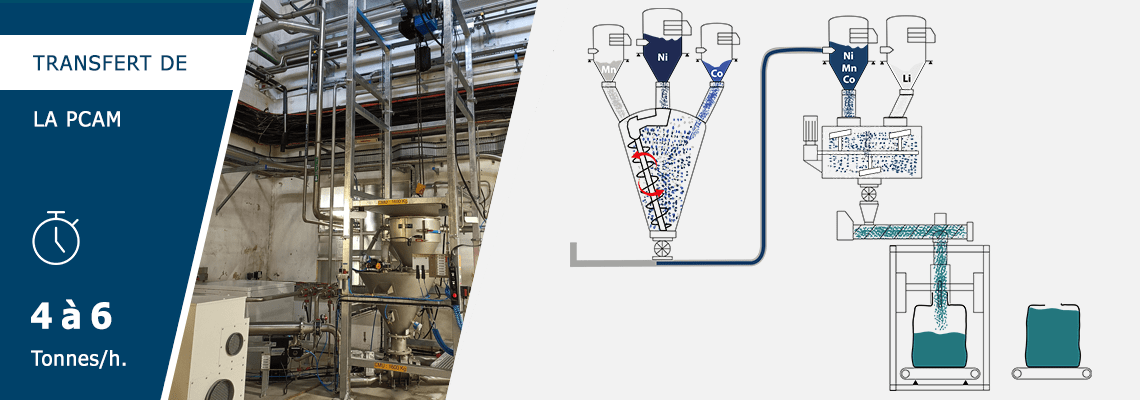
Automated CPTED preparation - PCaMatic®
Key features of the PCaMatic® process line
Contained design
Protects operators from exposure to toxic powders.
Mixing homogeneity
Guarantees consistent end-product quality.
Ceramic equipment
Prevents premature wear and metal ion contamination.
Automated packaging
Ensures safe filling of bulk bags.
Automatic conveying
Facilitates transport of bulk bags through the line.
Available PCaMatic® models
PCaMatic® 1
- Incorporates two weighed cyclones for lithium and metal precursors
- Equipped with ploughshare mixer with ceramic coating option
- Confined bulk bag filling station
PCaMatic® 2
- Adds a second upstream mixer
- Three additional cyclones for nickel, cobalt and manganese
- Pneumatic transfer to cyclofilter connected to second mixer
PCaMatic® 3
- Includes cyclofilter feed systems
- Confined bulk bag discharge station options (EasyFlow ®Flex)
PCaMatic® 4
- Replaces bulk bag filling station with bin filling unit
- Conveying and weighing of totes before transfer to furnaces
The benefits of PCaMatic® technology
Optimized safety
Confined design significantly reduces operator exposure to toxic powders.
Increased efficiency
Process automation ensures rapid, homogeneous mixing of components.
Flexibility
Different models adapt to the specific needs of each customer.
Product quality
The use of ceramic equipment and magnetic detectors guarantees the purity of the final product.
Regulatory compliance
The system meets strict safety standards and environmental regulations.
The PCaMatic® line from Palamatic Process represents a state-of-the-art solution for the battery industry, offering safe and efficient automation of CPTED preparation. By choosing this technology, manufacturers benefit not only from in-depth technical expertise and customization tailored to their needs, but also from ongoing support and constant innovation.
All these solutions enable companies to maintain high-quality production while protecting their operators and the environment, positioning Palamatic Process as a strategic partner in the evolution of the industry.