Loading of bulk bags of soda ash with high flow
Processed Material: Soda Ash
Our client, located in northern California, is a distribution and logistics company for the export of natural soda ash. The project was to construct a brand new, state-of-the art packaging facility for the wholesale distribution and export of natural soda ash in bulk bags.
Project Requirements:
- A high-rate bulk bag filling system that could be operated on a daily basis with only a few operators present.
- The target bulk bag filling rate is 120/hr with two different bag sizes, 1 and 1.25 metric tons.
- The super sack loading system needed to work in coordination with the rail car delivery system and 150 metric ton surge hopper (existing client infrastructure).
The goal of the bulk bag filling lines was to automate as much of the process as possible, including: bulk bag shaping, filling, weighing, removal, sealing and transfer to a buffer area.
The industrial Equipment Solution Palamatic Process :
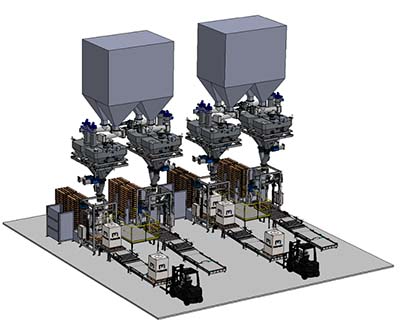
- Screw Conveyors
- Weighed Buffer Hoppers
- FlowMatic®06 – Automated Bulk Bag Filling System
- Controls and Automation
1. Screw Conveyors
At the beginning of our installation is the necessary mechanical conveyors (or screw conveyors) to help extract and transfer the soda ash from the primary surge hopper unit above the installation.
The tubular screw conveyors were chosen over standard rotary valves to reduce the overall height of the structure, as well as better powder dosing accuracy into the buffer hoppers below. Auger conveyors can be automatically controlled by fitting them with a VFD (variable frequency drive) and allowing other components such as load cells and level probes to communicate with the powder conveying equipment via PLC.
For this project, the screw conveyors were approx. 12.75” in diameter and 4 feet in length. The tubular structure and pitch were on a slight incline, therefore saving head room and height between the surge bin (above) and buffer hoppers (below). They conveyed the material at a rate of 39 metric tons per hour.
2. Weighed Buffer Hoppers
In order to hit a filling rate of 120 bulk bags per hour, the solution was to install 4 filling lines with 2 buffer hoppers for each filling head. With this method, one hopper was being filled with soda ash while the other one was filling the bulk bag below. By working with in tandem bulk material hoppers, the super sack filling operation below could work in sequenced time without interruption.
With this design method, the rate was doubled on each filling system line. The storage capacity of each buffer hopper is 1500 liters. The outlets of the hoppers were fitted with pneumatic slide valves for material flow control via PLC automation. Other integrated components included high level and low-level probes, load cells and air cannons. The level probes and load cells provide the necessary measurement devices to allow full automated control with no operator intervention over the hopper selection and fill operations.
The overall facility was an outdoor operation, but there was some protection from exposure to the elements with a covered roof structure. However, soda ash is hygroscopic and if kept in storage too long may experience flow issues like rat-holing or bridging. Therefore, the buffer hoppers also incorporated air cannons and vibrating bin aerators to help keep the material flowing should it become compacted or exposed to high levels of humidity.
In order to assist with the air to material volume balancing during the bulk bag filling sequence, a dust filter was incorporated on top of the buffer hoppers. This way we could safely evacuate any dusty air being displaced while the material is pouring into the bulk bag.
3. FlowMatic®06 - Automated Bulk Bag Filling System
Palamatic Process has designed a bulk material handling system for bulk bag loading operations that provide full automation over all operational sequences, with minimal operator intervention required. The FlowMatic®06 model delivers a turnkey solution for all necessary equipment stages involved, including: buffer storage, feeding, dosing, weighing, filling, densification and removal.
The complete powder handling system solution provides the necessary automation for this gross weighing operation. For the required overall 120 bulk bags per hour (30 bulk bags per hour, per fill station), the system was equipped with all the necessary features like pre-dosing weigh hoppers, inflatable containment seal, automatic bulk bag strap hooks, adjustable height via pneumatic cylinder, pre-forming fan for shaping the bulk bag, commercial weighing for certified resell of the filled packages, vibrating table to densify the soda ash and stabilize the bulk bag, pallet unstacker and motorized roller conveyor for transfer of the filled bulk bags.
The operation cycle is as follows:
- The pallet unstacker feeds a pallet onto the motorized roller conveyor.
- The operator hangs the bulk bag on the automatic hooks by the straps and connects the fill spout to the inflatable seal.
- The hooks lock and the seal inflates securing the bulk bag in place.
- The pneumatic cylinder lifts the bulk bag off the pallet to provide tension for optimal filling and shape.
- The fan shapes the bulk bag
- The by-pass valve on the fan switches from inflation mode to vent mode (this allows for the material to air volume balancing)
- The pneumatic slide valve opens and the filling of the bulk bag begins.
- The pneumatic cylinder gently lowers the bulk bag onto the load cells below.
- The vibrating densification table shakes the bag to help with stabilization and optimal filling.
- The load cells indicate to the pneumatic slide valve when the target weight is reached and closes the powder valve.
- The second vibration occurs to finish packing the material.
- The inflatable seal deflates and the automatic hooks release the bulk bag
- The motorized roller conveyor transfers the bulk bag to a sealing station for tying of the bulk bag spout.
- The bulk bag is conveyed to a temporary buffer storage area for removal by forklift operator.
Our commercial team did a timed study on all operational sequences (chronogram) and determined between the operator’s responsibility and automated controls of the system, each bulk bag had a total fill and transfer cycle of 2 minutes each.
Let us take a closer look at each functional component:
The filling head has an elastomer seal that can be inflated via the plant’s compressed air supply. It contains a pressure limit sensor to avoid damaging the seal. This enables the secure and dust tight connection to the filling spout on the bulk bag. It ensures that the spout will not slip off during the powder filling sequence.
The automatic hooks have an integrated motorized trackway to allow the rear hooks to move forward for operator ergonomics. Once the operator attaches the bulk bag straps to the hooks, they slide back into position and lock the straps in place.
The pneumatic cylinder is on a spring tensioning system. Before filling, the bulk bag is raised off its platform to allow the bottom and sides of the bulk bag to maintain optimal shape. As material fills the bulk bag the spring allows the bulk bag to be gradually lowered onto the pallet.
The inflation fan helps shape the bulk bag to prevent any wrinkles or creases in the fabric. This way there are no dead air pockets after the material fills the FIBC. Once inflated, a bypass valve switches over to a dust collection line to allow air and fine particulates to escape through the dust filter on the weighed buffer hoppers. The filters are connected to a compressed air tank that sends a pressurized blast of air through the filter cartridge to clean them and prevent material build up. The reverse jet pulse cleaning system is on a timed sequence and helps reclaim any powder that would potentially be lost to the filters.
The vibrating densification table utilizes two vibrating motors on opposing sides of a slotted metal structure. The table is retractable to allow the positioning and transfer of the pallet on the roller conveyor. The metal slots fit between the roller conveyor to come into contact with the pallet. As the bulk bag is filled and lowered onto the pallet the table vibrates causing the small air pockets between powder particles to escape, densifying the material. This helps optimally pack the capacity limits of the bulk bag as well as stabilize it to keep it from bending or folding over, preventing accidents and material spills.
The roller conveyor line helps transfer empty pallets to the bulk bag filling head, as well as the bulk bag on its pallet, once filled. It begins with the pallet unstacker, which was designed to accommodate pallets of 2 different sizes. The overall magazine capacity was built to hold up to 20 pallets at a time. Each line was equipped with 2 pallet feeders, for a total storage capacity of 40 pallets that allowed for an hour of run time without reloading the pallet magazine. Two vertical indexing carriages mounted on slides and activated by pneumatic cylinders, provide the up and down movement and the three positions necessary for the lifting and unloading of the pallets. A guide rail structure pushes the pallets out of the unstacker and onto the roller conveyor. In addition, this pallet feed system is delivered with the following features: 2 inductive sensors for the front and back fork positions), 3 inductive sensors for the low, middle and upside fork’s positions and 1 photoelectronic sensor to indicate a pallet’s presence on the roller conveyor.
The motorized roller conveyor then transfers the empty pallet to the filling station. The load capacity of the mechanized conveyors is 1.2 tons per meter (3 feet) and the total length is 1.35 meters (about 4.5 feet). Once the bulk bag is filled, the conveyor pushes the bulk bag on the pallet to a gravity roller conveyor. By utilizing gravity roller conveyors, the plant can save on the system’s energy requirements. At the end of the gravity roller conveyor are regulator rollers to help slow down the speed of the bulk bag, as well as a pallet separator to single out each pallet for removal by a forklift operator.
4. Controls and Automation
The PLC was designed by our inhouse automation and electrical team. The control cabinet was made of an epoxy coated mild steel with a 7” touch screen. The PLC was made of Allen Bradley components, Micrologix 850 with ethernet connection. One main PLC control board and 4 local control boxes were outfitted on this system. Palamatic Process also offers remote diagnostic capabilities by integrating an ethernet remote maintenance box. This allows our team to remotely diagnose and troubleshoot any system errors or malfunctions in real time. Palamatic Process designs, assembles and programs all controls panels in-house. Our team of automation engineers include user friendly raw material inputs, lot traceability, operator identification and dosing reliability. The PLC handles and controls the bulk bag filling, loss-in-weight dosing management, conveying, dust collection, feeding and hopper selection. Our technicians are also available for on-site commissioning and training support.
Palamatic Process has been supplying the powder and bulk solids industry with bulk bag handling equipment since 1992. In order to determine what solution is best for your project, contact one of our sales engineers. Together, our team of experts can provide the right kind of powder filling equipment that will meet your production goals.
Contact one of our experts today for assistance with needed material handling solutions and to request a quote.