Processed product: cement
Cement truck filling
The installation concerns two EasyFlow® EF100 bulk bag unloading stations for high-speed semi-automatic unpacking.
The main advantage of this double station is that it works in masked time.
Utilizing four entry areas, two full bulk bags can be staged and loaded while two more bulk bags are being emptied.
With this automated operational sequence, it is possible to achieve very high bulk bag emptying rates.
Each station includes:
- Two lifting hoists
Installed on a guiding rail to allow movement of the bulk bags towards the unloading area.
- Two automatic handling crosses
- This system guarantees optimum emptying without loss of product or operator intervention.
- A bulk bag massage system
The pneumatic jacks break up bridging and mass flow issues.
- A "U" shaped bag punctures point
This puncture blade allows the cement bulk bag to be opened mechanically without direct action by the operator.
The force exerted by the 'product' weight on the knives allows instant cutting of the bottom of the bulk bag and free-flow of the cement into the hopper below.
- A collecting hopper with a capacity to store two whole bulk bags (common to the 2 emptying stations).
- A cylindrical dust collection unit
The dust is collected from the air flow by filtering elements inside the hopper via the integrated compressed air cleaning system. This industrial dust removal system is specifically adapted to cement production units.
- A 60 ton/hr dense phase pneumatic transfer system with bypass (common to the two emptying stations).
The working environment is guaranteed to be dust-free thanks to the completely sealed transfer airlock.
- A tubular transfer screw
This equipment allows the mechanical transfer of the cement to the truck loading sleeves located on the platform
- A truck loading spout
This telescopic loading sleeve ensures the continuous loading of cement into tanker trucks.
An access platform allows operators to safely perform maintenance on the truck loading spouts.
An electrical control cabinet with touch screen allows access to all parameters and individual equipment.
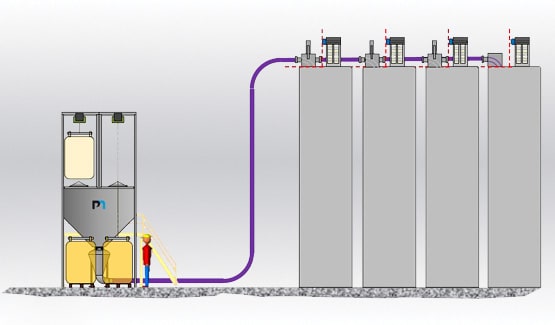
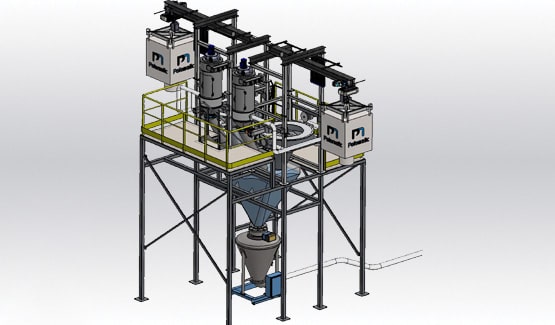
The automatic operating cycle is as follows:
- Once the bulk bag handles are positioned on the handling cross, it is automatically taken to the unloading area.
- The operator then controls the operations via the control cabinet.
- The hoist allows the bulk bag to be lowered to the level of the puncture point. The weight of the bulk bag exerts pressure on the tip which causes the bulk bag to be cut open.
- The cement then empties into the collection hopper.
- Once the bulk bag has been emptied, the hoist automatically returns to its initial position.
- The operator detaches the bulk bag handles from the hoist and the following sequence can start over.