Processed powders: silica, wheat, carbonate
Premix manufacturing
The installation consists of a new mixing line for the production of natural additives for animal nutrition. The raw materials are brought in bulk bags, sacks and pots.
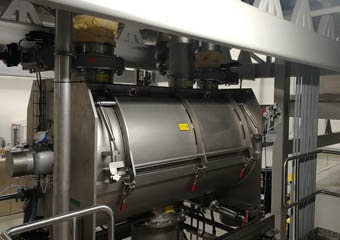
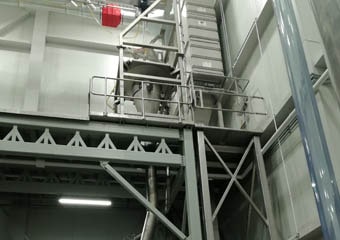
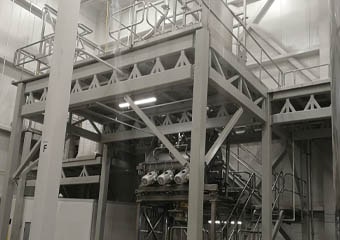
Three bulk bag unloading stations, equipped with electric hoists, installed on the 2nd floor mezzanine. The first station is dedicated to silica powder with special precautions taken into consideration. For example, to enhance operator safety a dustproof docking system, gloves box and dust suction booth have been integrated into the station design.
A second station, installed adjacent to the first, allows the discharge of bulk bags of other bulk materials such as carbonate powder. This station is also designed to allow operators to dump 25 kg sacks and pre-weighed ingredients. A scale is located on the same level, with integrated suction booth for dust control, allowing the operator to pre-weigh these bulk ingredients.
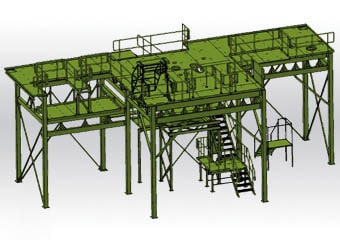

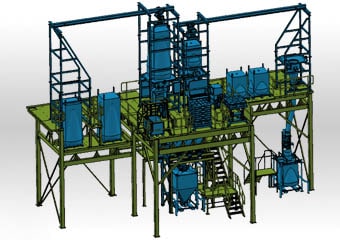
These two stations feed a mixer, located on the 1st floor below, via rotary valves which provide a controlled feed with accuracy of +/- 1 gram and overall batches totaling 2,200 lbs. During the blending phase, essential oils such as orange peels are introduced. The blend is then transferred to 2,000L stainless steel containers, located on the ground floor level of the plant.
A third bulk bag unloading station also allows the operation of filling containers directly in case mixing is not required.
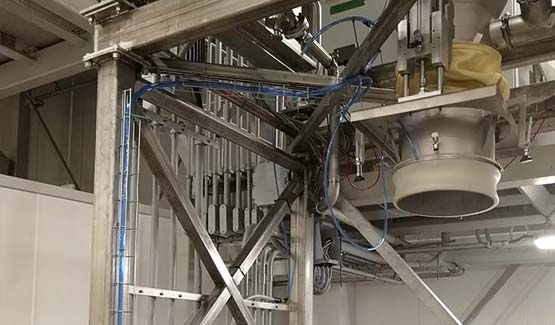
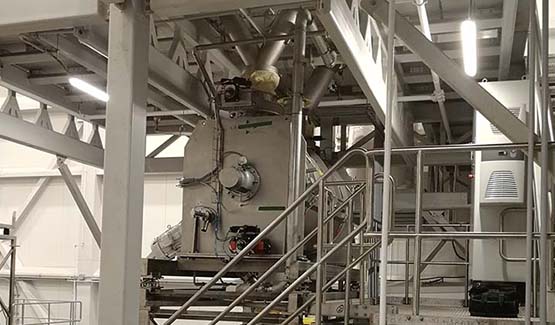
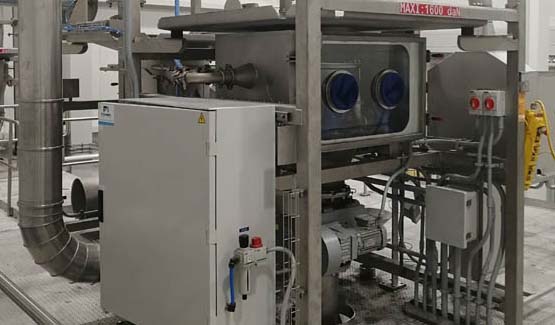
These IBC stainless steel containers are stored and when required, installed onto an unloading station where the product is transferred to a FFS machine.
All bulk handling equipment (bulk bag unloading, mixing and IBC filling stations) are connected to a centralized dust collector to provide a clean and healthy atmosphere.