Processed material: wax, parafin
Shampoo manufacturing
Our client is the world leader in hygiene and beauty supplies.
The installation consists of three EasyFlow® bulk bag discharging stations with integrated dosing (by load cells) and a VFlow® pneumatic vacuum conveying system.
The complexity of the installation lies in the handling of wax powders which tend to stick and clog at a low liquefaction temperature. As the loading points are located on the melters, the powders are subject to high temperatures and humidity.
The Palamatic Process installation integrates specific devices to avoid rising humidity and protect the temperature migration to the conveying cyclones. As the materials are stored in bulk bags, lumps are present in the powder due to compression. In order to ensure an autonomous discharging of these bulk bags, pneumatic massaging systems as well as knife lump breakers are integrated on the bulk bag stations.
In addition, a bulk bag tensioning system is installed on the handling cross. The compensating cross prevents the bulk bag inner bag from slipping and helps the product flow by avoiding the creation of retention " pouches ".
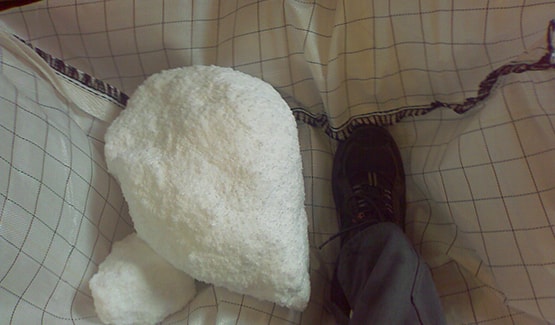
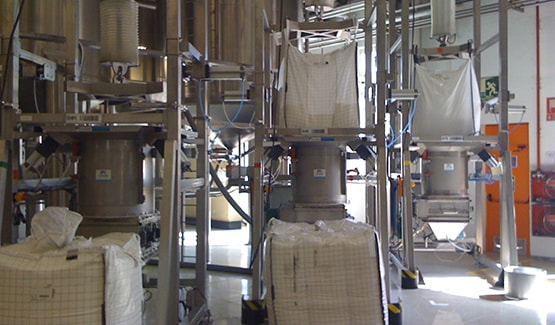
Concerning the knife lump breakers, a specific design has been implemented to compensate for the "waxy" nature of the product. The knives are of a specific shape with a lower rotation speed and a removable calibration bar to ensure that the equipment is not clogged.
The loading of the melters is carried out in batch mode with weighing management by the installation of scales under the bulk bag station. The pneumatic conveyor is directly controlled by the load cells which provides compliance with the recipe by weighing the bulk bag.
Pneumatic vacuum conveyors incorporate an automatic purge cycle to ensure accurate weighing and also prevent clogging of the pipes.
All equipment is made from 304 stainless steel.
Palamatic Process has designed many installations for the loading of melting reactors with different types of powders (wax, resin, dioxide...).
Each installation is customized according to the technical specificities of our customers.
Contact us to design together your next process line for your powders and bulk solids!