Processed powders: gluten and starch
Handling of food starch
Our client specialized in the conditioning of bulk products and raw materials.
Palamatic Process has developed a high speed bulk bag packing line with strict hygienic design standards. The purpose of the process is to condition the bulk material, which is fed from the truck to the buffer hopper, in bulk bags.
The raw material, with a grain size density of 500 kg/m³, is collected in a receiving cyclofilter, a 3,000 liter 304L stainless steel buffer hopper and a 20 m² dust collection filter and an indoor explosion vent.
Preparing bulk bags
A pallet unstacker feeds the bulk bags filling station automatically and without operator intervention. It can hold between 15 and 20 empty pallets and has a throughput of 250 pallets per hour. The pallets are loaded with a forklift truck by an operator.
The pallet unstacker is designed for installation on motorized roller conveyors to automatically dispense pallets to the bulk bags filling station located in a clean room.
Once the pallet is in position, the operator installs the FIBC on the automatic rotary hooks positioned on the upper part of the structure which are controlled by the PLC.
A bulk bag filling platform with a tilting railing provides easy access to the upper part of the bulk bag filling machine for hanging the handles and closing the bulk bag filling chute. This platform ensures ergonomic access to the super sack for the operator.
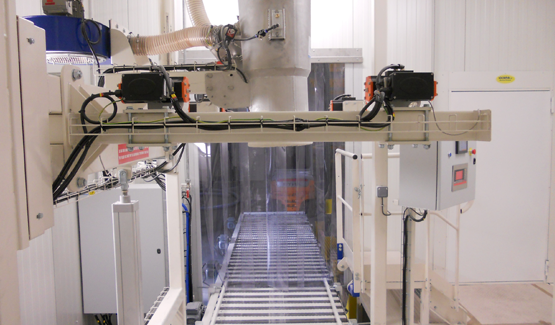

Metering and filling of the big bags
The bulk material is introduced into the receiving cyclofilter by means of a blower. The bulk material is then cycloned for air/product separation. The high efficiency filter, integrated into the conveying cyclone, ensures the final separation of the air. A compressed air cleaning system is used to clean the filter at each pneumatic conveying session. Vibrating fluidizers are positioned on the buffer hopper to prevent the materail from bridging and optimize its flow.
The material passes through a 30 m³ per hour rotary airlock valve with ATEX 22 motorization for controlled dosing and an ATEX 20/22 GSC 900 vibrating screen. The vibrating screener protects the equipment that compose the packing process by eliminating potential agglomerates and potential foreign bodies.
A flexible connector isolates the bulk bag filling station from the vibrations of the vibratory screener. Its design allows it to be quickly installed and uninstalled without tools. The set consists of two stainless steel connectors and a flexible polyester (food grade) hose connection.
To stop scrap metal bits, a double-stage magnetic grid separator is mounted under the sealed connection system. It is cleaned by opening the drawer.The bulk material then flows into the FlowMatic® 02 big bag filling station, which consists of a double-walled filling tube, a connecting inflatable seal, a tension cylinder, a height-adjustable structure to suit different bulk bag sizes and load cells to ensure commercial weighing.
The pneumatic tensioning cylinder is operated by the control cabinet, which adjusts the hanging height and deposits the bulk bag on the pallet as it is filled. This sequence provides optimal filling and excellent stability of the bulk bag on its pallet.
A vibrating table with airbags is mounted on the roller conveyor and is retractable to avoid interference with the conveyor. This component optimizes the security of the bulk bag on its pallet as well as homogeneous filling of the bulk bag.
Removal of the big bag
Once the bulk bag is filled, the inflatable seal deflates, the loops are automatically removed and the FIBC is removed with its pallet by means of the motorized roller conveyor. The storage conveyor for filled big bags has a capacity of 4 units.