Process products: wheat bran, wheat flour, disinsected wheat bran
Unloading big bags containing grains and cereals
- Product reception workshop -
This installation makes up phase 1 of a production and processing unit for insect larvae.
The complete production and transformation line consists of the breeding and processing of insect larvae for livestock feed, aquafeed, petfood, fertilizer, etc.
The larvae are introduced into a vertical farm which is fully automated: control of the living environment, feeding (enlargement / breeding process) and sorting of insects makes it possible to harvest mature larvae.
Once they reach maturity, 95% of the larvae are harvested and moved to the processing stage while the remaining 5% are reintroduced into the process give birth to a new generation. The vertical farm is therefore autonomous.
After processing, insect proteins are represented in the form of powder or oil.
This process, called bioconversion, also develops with the production of animal proteins for human nutrition. The droppings (frass) are used in the formulation of fertilizers for soil nutrition.
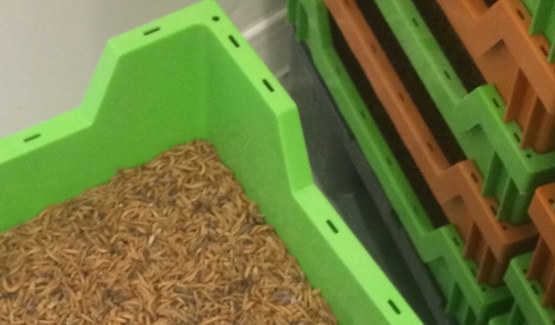
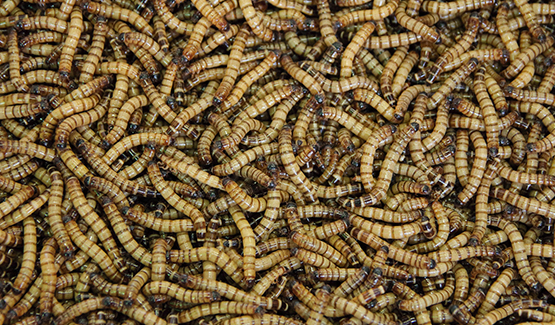
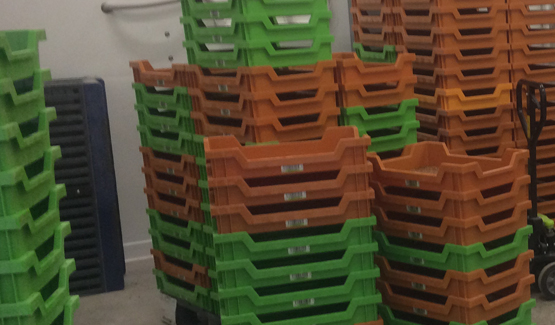
The objective of this first workshop is the creation of substrate to feed the growth tanks.
A DUOPAL © combined station allows the unloading of big bags and sacks within the same station and is designed to be Atex 20/22 certified.
This big bag emptying station aims to feed insects (larvae and adults) with dry raw material (bran). An electric hoist does the handling and loading of the big bag.
A sack tip tray is integrated into the big bag emptying structure, allowing the introduction of small quantities of food packaged in 50 kg sacks (flour). This integrated bag dump design makes it possible to introduce materials that are not available in big bag containers.
The entire unloading station is connected to an independent dust filter, which is shared with a sorting workshop that makes up the overall production unit. The fines from the dust collector are then evacuated by vacuum pneumatic transfer to the waste treatment room.
At the hopper outlet, an ATEX 20/22 tubular transfer screw provides a controlled feed rate to the rotary sieve. The transfer rate is 2600 kg/hr with a product density of 0.2.
In order to "secure" the feeding process, a centrifugal sieve and a pest control system are installed downstream from the emptying station. The output powder is conveyed by high pressure pneumatic transfer (diluted phase) to the mixing line.
This ROTARY centrifugal sieve ensures "process safety" of the supply line. The product to be screened is fed to the cylindrical sieve by a small feed screw. The connection between the screw and the screen is ensured by a flexible sleeve, which provides a dust tight seal between the 2 pieces of equipment.
Centrifugal force throws the product against the mesh of the screen, which the rotating blades do not come in contact with. The blades project the product through the screen mesh and provide a de-agglomeration effect on soft lumps and agglomerates. Any oversized or tramp material is evacuated at the end of the sieve via the rejection / overs port.
The centrifugal sifter "cleans" the powder of any living foreign objects.
At the exit of the process, a rotary sluice allows the extraction and the dosage of the product in the compressed pneumatic transfer circuit. A gearbox ensures the introduction of the product into the transfer circuit.
The whole of this unit is connected to the common dedusting system, located in the sorting workshop. The Duopal® station (unlacing box and bag dump) as well as the degassing connections of the rotary lock (pneumatic transfer) are connected to the dust collector.
This ATEX dust collection unit is installed indoors (flame suppressor box).
This set composed of a combined Duopal® emptying station, screw, sieve, and pneumatic transfer system is ATEX 20/22 certified.