1. Production and design parameters to consider
The choice of a bulk bag station will depend on several elements:
- Bulk bag characteristics
- Constraints related to the product / treated powder
- The type of production needed (transport, storage, discharge, packaging)
- The requirements of the manufacturing process: desired rate, gross or net weighing, transport and conveying, degree of automation, atmosphere in the production area (explosive or not), etc.
- Constraints of the industrial sector
- Construction materials for the bulk bag structure as well as space constraints
- The need for additional process equipment
Process Palamatic has a wide range of bulk bag stations to address the problems of filling bulk bags and unloading bulk bags of manufacturers. We also offer integrated options (e.g., loading mechanisms of bulk bags, buffer hoppers for bulk bags, bulk bag compactors, etc.).
These features offer the following advantages:
- To ensure safe handling and protection of operators
- Adapt to all types of bulk bags
- Reduce dust emissions (possibility of total containment)
- To extract or package products with poor flow properties
- Adaption to different industrial sectors such as chemicals, food processing, fine chemicals, construction, energy, etc.
2. Bulk bag filling station
To fill the bulk bags, various stations ranging from standard equipment to fully automated production lines are possible.
The FlowMatic® 01, FlowMatic® 02 and FlowMatic® 03 stations allow economical and ergonomic bulk bag handling, while ensuring total containment of your powders.
For manufacturers looking for high throughput, the FlowMatic® 04 and FlowMatic® 06 filling machines are ideal.
Some packaging systems are dedicated to handling certain powders. This is the case with the FlowMatic® 02 AshFlow bulk bag filler, designed for loading fly ash on thermal power plant sites. Another example is the FlowMatic® 03 Care specially manufactured for the packaging of fragile products.
Mobile packaging of bulk products at multiple feed points is possible with the FlowMatic® 07 model. It is a station particularly suitable for loading below silos or by truck loading spouts.
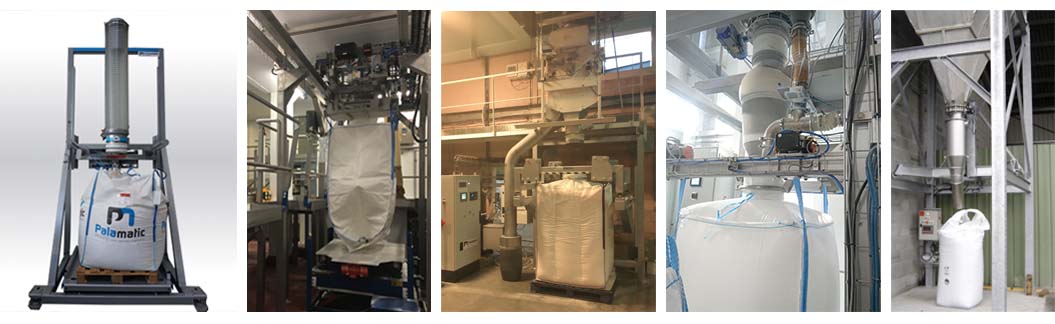
For bulk bags with one handle, two bulk bag station designs are available: FlowMatic® 08 and FlowMatic® 09 . One design is expressly suitable for large tonnage packaging, for example the cereal, quarry or fertilizer industries; while the other is an efficient solution for automatic net weighing operations.
Hygienic versions of bulk bag filling machines in our Easy Clean range have been designed for sectors with demanding standards such as the food or the pharmaceutical sectors. This is the case with the FlowMatic® 05 and FlowMatic® 10 references .
Palamatic Process also offers personalized and tailor-made bulk bag filling solutions that can integrate functions such as Clean In Place (CIP), workstation ergonomics, extraction of difficult products, reduced installation height, etc.
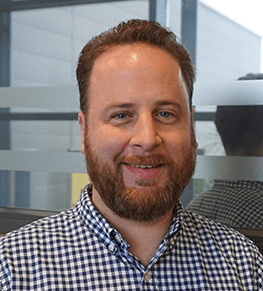
Looking for a big bag station? I am
available to advise you in your study.
Chris, powder expert
3. Bulk bag discharging station
Regarding bulk bag unloading operations, there are also various possible designs depending on your needs and constraints. The EasyFlow® range consists of:
- Bulk bag standard unloading (EasyFlow® EF0)
- Confined with telescopic tube ensuring a dust tight and hygienic process (EasyFlow® EF1)
- Contained with an integrated glove box for the handling of toxic products while offering operational ergonomics (EasyFlow® EF2)
- High production rate through automation of the unloading cycle and compaction of empty bulk bags (EasyFlow® EF100-200)
- Full automation via loading crane gripper, no need for operator intervention (EasyFlow® EF500)
- Multi-product partial unloading via suction cane (EasyFlow® Flex)
- Tailor-made adapting to your specific needs and constraints
Deconditioning equipment that meet the needs of manufacturers loading their process with bulk bags and various containers (50/100 lbs.) on the same unloading point are available.
As for loading methods for bulk bag and bag dump machines, several options are available with the use of an electric hoist, forklift or overhead crane:
- Bulk bag and sack vacuum station with stripping box (Duopal® DP0)
- Bulk bag and sack unloading station with telescopic tube (Duopal® DP1)
- Bulk bag and sack discharging stand with glove box (Duopal® DP2)
In addition to the bulk bag unloading station, equipment such as a bulk bag compactor, a dust collector or even a bulk bag handling cage can be added according to your process requirements (recycling of bulk bags, control of dust emissions, poor material flow properties, etc.).
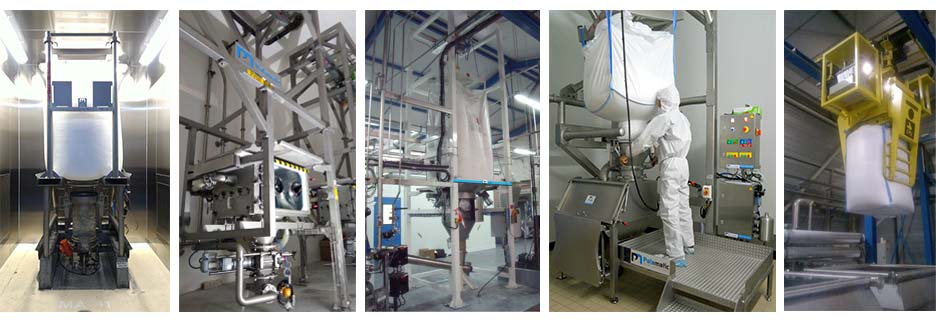
Contact our experts to choose the most suitable filling or discharging bulk bag equipment that meets your process specifications.