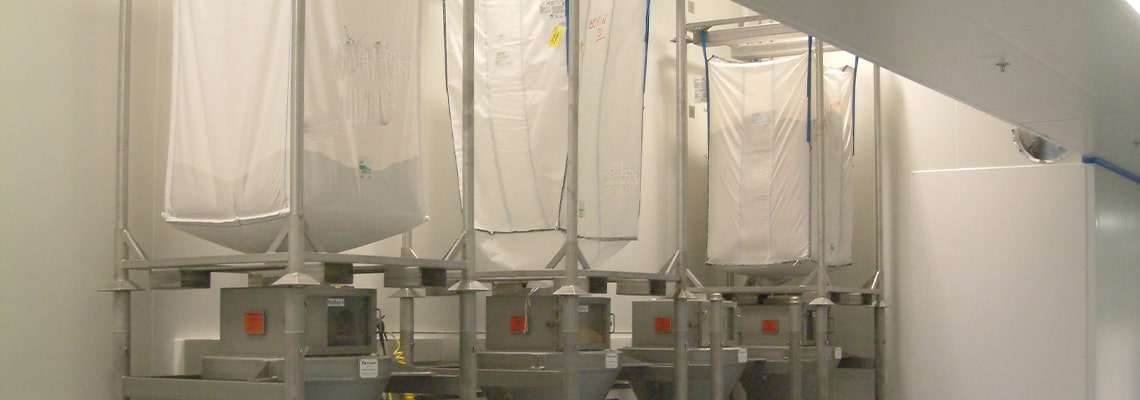
Bulk bag unloading systems are widely used in industries handling ingredients in the form of powders and bulk solids. These emptying installations make it possible to considerably reduce the number of manipulations by production operators.
Before selecting your FIBC emptying system, it is important to identify the 5 key criteria that will guide you in your decision making.
Criterion #1: How do I position my bulk bag on the unloading station?
Handling bulk bags imposes safety rules due to the weight handled - generally between 800 and 1,500 kg.
4 main options are available to you:
- Handling of the bulk bag by forklift via a handling cross.
- Handling by an electric hoist fixed to the structure of the bulk bag vacuum station
- Handling by your workshop crane via a specific handling cross.
- Handling of the bulk bag via a handling cage
1. Handling of the bulk bag by forklift via a handling cross
The handling of the bulk bag by forklift is carried out using a handling cross, which allows hooking of the handles of the bulk bag. When the super sack is attached to this handling cross, the lift truck positions the assembly on the unloading structure. To facilitate removal, centring systems facilitate positioning. In this bulk bag discharging configuration, only authorized operators are able to place the bulk bags. Production operators are therefore dependent on the flow of forklift drivers. Another advantage of the bulk bag unpacking station with forklift loading is the low cost.
2. Handling by an electric hoist fixed on the structure of the bulk bag unloading station
For the electric hoist solution, the loading of the FIBC is autonomous for positioning on the unpacking station. The electric hoist requires an annual maintenance check but offers great flexibility of use and maximum safety. Bulk bag emptying with an electric hoist represents the majority of installations. The other advantage of bulk bag unpacking stations using electric hoists is their total adaptability to all bulk bag dimensions. Thanks to the electric hoist, the operator positions the bulk bag on its deposit tray regardless of its height.
Several electric hoist options exist such as: automatic piloting, reduced design height, ATEX version, wireless remote control, high lifting capacity, etc.
3. Handling by your workshop overhead crane via a specific handling cross.
The use of your workshop overhead crane to place the bulk bag on the emptying station requires the use of a specific handling cross to avoid “monopolizing” the crane. Once the bulk bag is positioned on the deconditioning station, the bridge operator will be able to release the bridge hook via the specific Palamatic slag. Using the bridge offers the possibility of picking up the bulk bag to discharge over the entire area covered by the bridge. However, this economical configuration implies lower loading rates and is generally used for installations which do not require frequent changes of bulk bags.
4. Handling of the bulk bag via a handling cage
The bulk bag handling cage is mainly used in sectors with high hygienic constraints. Manufacturing processes that do not allow pallets in the production area will favor this type of loading. The operator will first position the bulk bag in its handling cage, then take this assembly (cage + bulk bag) to the foot of the unloading station and then position it on the emptying structure via an electric stacker. This configuration of bulk bag deconditioner is mainly used in the pharmaceutical field where hygiene is the main constraint and deconditioning rates remain moderate.
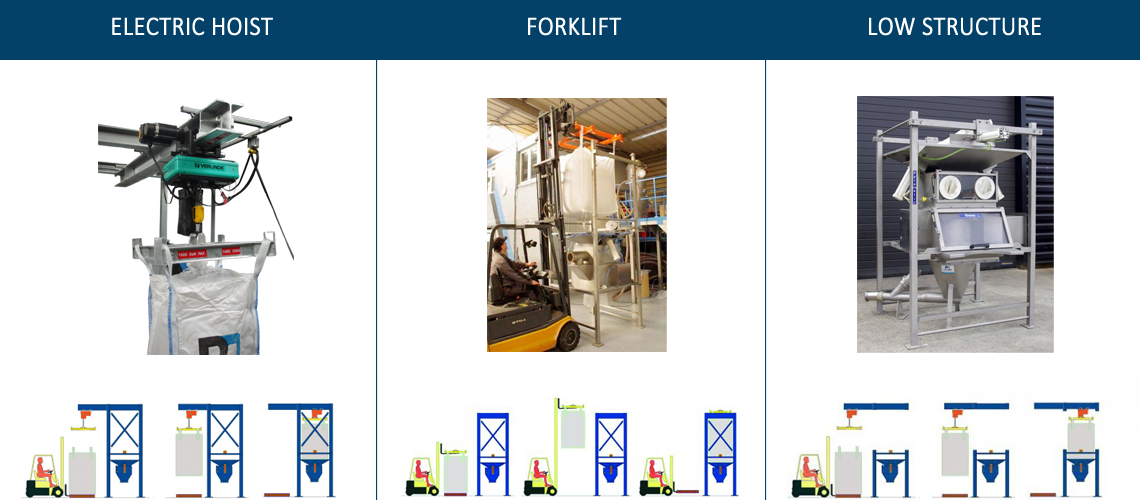
Criterion #2: Bulk bag with or without discharge sleeve?
There are two main categories of bulk bags: with discharge cuff and so-called “full-bleed” bulk bags, i.e., without cuff / without discharge chute.
When the bulk bag is equipped with a discharge spout, several solutions are available to you (see criterion #3).
When the bulk bags handled are full bleed type, it is essential to provide a bulk bag puncture blade on your emptying station. This puncture tip allows the bulk bag to be cut open as soon as it is positioned on the station. This bulk bag puncture point must be particularly sharp and pointed to ensure a clean opening without generating frayed fabric, and sufficient penetration to ensure the flow of the most difficult products.
Palamatic adapts the bulk bag cutting tool according to your products. Ask our bulk bag experts for advice.
Criterion #3: How to open the cuff of the bulk bag?
Opening a bulk bag requires you to untie its discharge sleeve . Several solutions are available:
- Open the cuff in a untie box
- Open the cuff through a glove box (avoids operator exposure)
- Connect the cuff to a telescopic clamping tube
The opening method directly influences operator ergonomics during this phase.
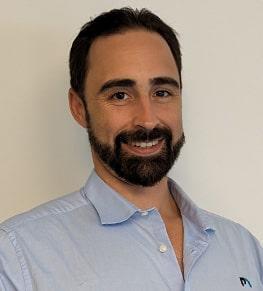
If your require further assistance,
I am at your entire disposal.
Tarik, powder expert
1. Open the cuff in a untie box
The unlacing box offers the greatest ergonomics with few constraints on the geometry of the cuff. All bulk bag cuffs can be opened on this type of installation. The box is at the operators height and has complete visibility allowing the product to flow as soon as the cuff is released. The flow of powder at the bulk bag outlet is channelled into a containment tube, also known as an “anti-overflow” tube.
2. Open the cuff through glove box
To avoid operator exposure to the material during opening of the bulk bag, Palamatic Process can make use of a glove box. This solution, particularly used for toxic materials, offers total containment of the material but with less dexterity for the operator. Working with gloves can hinder the untying of the spout on the bulk bag. In this configuration care must be taken to have sufficient lighting for the unlacing box, an ergonomic access height and bulk bags with a simplified B-lock type opening system.
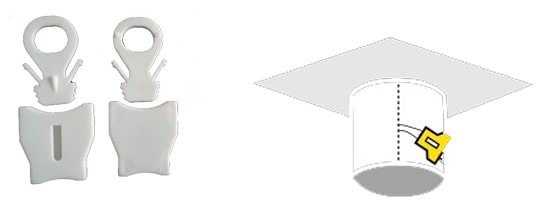
3. Connect the cuff to a telescopic tube
The bulk bag connection tube is the solution to ensure a clean drain without contact with the outside atmosphere and the material! However, this solution requires the use of specific bulk bags. The bulk bag emptying cuffs must be long enough to allow the connection to the tube. The "free" cuff under the knot must be long enough to connect to the clamp before untying it. Likewise, bulk bags made with an internal liner must be tied in a specific way.
Our bulk bag handling experts will be able to guide you in the selection of your bulk bag. The bulk bag unloading solution with connection tube is becoming a popular choice due to the following advantages: cleanliness, ergonomics, optimization of the flow produced by continuous tension of the bag, etc.
The Palamatic test center integrates all the bulk bag opening solutions, which allows you to come and test the best configuration adapted to your needs and constraints.
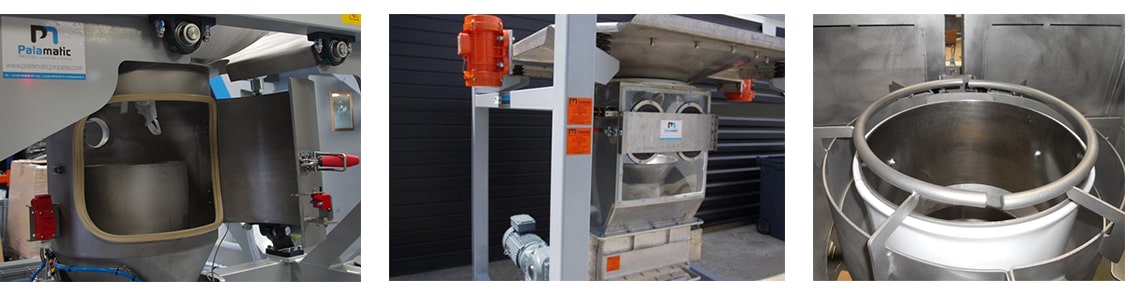
Criterion #4: Is my product fluid, flowing, arching, cohesive?
Choosing a bulk bag station means defining the product to be treated, and therefore, the flowability of this powder. Palamatic bulk bag vacuum stations incorporate many options to facilitate product flow.
The standard bulk bag deconditioning station can integrate pneumatic or hydraulic massage systems as well as a vibrating plate. These two systems promote the flow of cohesive powders.
The vibrating plate allows the extraction of powders similar to of the vibrating bottoms of silos. The vibration of the bulk bag makes it possible to agitate the material, or even to collapse arches that may form.
The pneumatic massage cylinders penetrate the heart of the bulk bag for strong mechanical action. This solution is generally used for powders with the most difficult flow properties. The bulk bag massage can be carried out by two or four jacks depending on the size of the bulk bag and the rate of compaction of your powders.
Still in doubt? Go to our Palamatic test center to validate the option to choose!
Criterion #5: Generation of dust
Opening a bulk bag generates dust! Integrating a filter, a dedusting ring or a complete enclosure of the station are questions to consider.
Is your powder of light density? It is important to connect your emptying station to a centralized dust collector in order to capture fine particulates. The connection to the dust collector is made at several collection points with adjustment of the suction flow rates by register.
For bulk bag emptying installations that operate with a high emptying rate, the station enclosure may be the best option. The discharge of large volumes in a short time generates exchanges of large volumes of air and potentially a lot of dust. The Palamatic bulk bag emptying solution, model EF500, offers a cowling of the entire station with a connection to the centralized dust collector and even compacting of the emptied bulk bags.
Why trust our experts?
Emptying bulk bags is a simple operation when the equipment used meets your constraints. Using a badly designed bulk bag vacuum station represents a safety risk. The equipment can be a source of pollution in your production workshop, and potentially cause your products to be poorly unloaded.
Working with a Palamatic station designed and manufactured by experts in bulk bag handling is a guarantee for the success of your project.