Manufacturers that handle dry ingredients in their processes are subject to flow problems caused by caking, agglomeration, lumps or blocks of powdered materials.
Palamatic has developed a range of solutions to eliminate the presence of lumps and agglomerates.
Depending on your process, the lump crushing solution can intervene at several stages: entering the production line, during production or leaving the line.
For solutions at the entry point of the production line, bag dump, bulk bag discharging or silos can integrate lump breakers with double or single shaft knives.
1. Knife lump breakers
Knife crumbling solutions are particularly suitable for "exploding" lumps present in your materials as soon as they are incorporated into your process.
Products such as sugar, citric acid, sorbitol, salt, urea and all products in the form of powder are compatible with this lump breaking technology.
For sensitive products ("soft" product, low temperature fuse), a low blade speed should be implemented to avoid a risk of overheating and / or the integration of a single shaft lump breaker.
The knife lump breakers from the Palamatic range, EC® lump breakers, are available in several versions and offer different options. An ATEX version with specific motor, temperature control and nitrogen purge can be offered.
Likewise, a calibration grid positioned between the knives makes it possible to reduce the size of the agglomerates at the outlet. In food grade applications, this grading comb can be designed for easy removal to facilitate the cleaning phases of the lump breaker.
Palamatic offers three sizes of knife lump breakers: EC®30, EC®50 and EC®70. The flow rate desired by your installation must be in accordance with the size of the lump breaker (see the sizing guide).
Single shaft and double shaft knife lump breakers can be installed under load under your storage hoppers or under dosing equipment (transfer screw, vibrating corridor, etc.).
2. Granulators with calibration grid
Unlike knife lump breakers, sizing granulators are particularly suitable for removing medium sized clumps and friable clumps while providing consistent particle size control.
The rotating blades granulators are very often installed in the hoppers of vacuum bags. This layout configuration makes it possible to ensure a supply of product free from agglomerates. The calibration grid on the granulator is removable and interchangeable to adapt to the basic grain size of your product. This crumbling solution is implemented on processes consuming IQF food products. In these specific applications, several granulation grids are provided to adapt to the cut size of the products (onion, rice, carrot, tomato, zucchini, etc.).
Discover an application of IQF product crumbling.
The Palamatic range incorporates three standard models offering a wide range of kibbling flow rates. To select the best solution, come and test your product in our test center equipped with granulator, lump breaker, crusher, pin mill, etc.
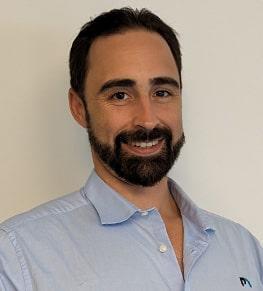
Do you need personal advice?
I am available to accompany you.
Tarik, powder expert
3. The rotating blade devourer
The anti-bridging device or rotating blade separator represents an interesting alternative between crumbling solutions and flow aids.
The pale stripping solution is implanted in the storage hoppers and allows forced extraction of the product. In order to break the possible solidification of the stored product, Palamatic integrates a fixed blade equipped with a comb thus making it possible to break up the lumps created by storage.
For difficult products, several blades can be installed in a staged manner to accentuate the extraction force.
4. The bulk bag crusher
The bulk bag crusher is the solution specially designed and entirely dedicated to solidified bulk bags.
Products stored in jumbo bags, which are subjected to compression from being stacked in storage or transport, can have a very high compaction rate. The bulk bag crusher destroys the caking by a mechanical massage action. Hydraulic arms act like jaws to break up the big bag for efficient emptying operations. The massaging energy put into play by the hydraulic system amount to more than 60 tons of pressure! This percussion force guarantees the breaking of solidified materials, resulting in the free flow of the powder as soon as the bulk bag is opened.
5. The rotary finger lump breaker
Extremely compact, the rotary finger lump breaker is easily installed at the outlet of a vibrating conveyor or at the inlet of a rotary lock.
Designed as a butterfly valve, the rotary finger lump breaker attaches to standard DN-PN type flanges. The Palamatic finger lump breaker range covers DN150 to DN250 flanges. The applications of these compact lump breaking solutions are often in the food or pharmaceutical industries with products that contain friable lumps. The use of the finger lump breaker avoids any risk of blockage at the entry of a screw conveyor, or when loading material into a vacuum pneumatic transfer.

Overview of the 5 capping equipment