Description
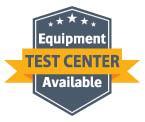
AUTOMATIC BAG DUMP STATION - MINISLIT® - Automatic opening without any adjustment
The Minislit® Automatic bag dump station has a special profile cutting system without shredding to open the bags on three sides. The principle of turning and emptying the bags ensures a maximum emptying rate.
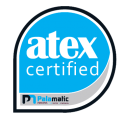
Designed to open bags of powdery products, bulk, powders, the Minislit® automatic bag vacuum is available with a belt cutting system. Suitable for multiple applications, from aggregates to pharmaceuticals, the integrated parts of the Minislit® bag opener can be cleaned manually or mechanically using the "Cleaning In Place" (CIP) option providing a complete wash with drying (30 minutes between washing and drying).
The Minislit® bag dump station offers a bag opening rate of 2 to 8 bags/min.
The mechanical drive and guiding parts are located on the outside of the machine to limit wear and tear and offer the possibility of emptying products with a high degree of abrasion.
The MiniSlit® equipment can be integrated into an automatic bag opening process line such as our DePalSack® line.
-
Rate4
-
Overall dimensions5
-
Hygiene5
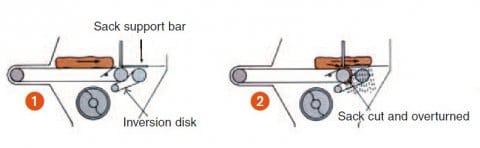
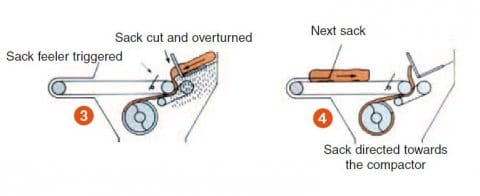
Operation procedure:
1. Deposit of the bag on a roller conveyor, positioned laterally to the bag dump station, for its introduction into the body of the machine on the screen provided for this purpose
2. The presence of the bag is detected by the sensor that controls the cutting system
3. The blade cuts the bag and the lower part is grasped by the inversion discs for complete emptying
4. When the sensor is deactivated, the blade moves up to the rest position so as not to cut the bag in half
5. The bag is directed towards the bag compactor through a helical screw and the machine is ready to receive the next bag
Equipment advantages
- Automatic ribbon cutting system
- Bag manipulator and belt conveyor
- Screw compactor for empty bag evacuation and dust emission reduction
- External gearboxes
Media
View our equipment in videos
Automatic bag dump station - MiniSlit®
Designed to open bags of powders and bulk materials, the automatic Minislit® 3000 bag discharging station is available with a belt cutting system.
Automatic sack discharging - Minislit
Automatic sack discharging - MiniSlit®
Automatic sack station MiniSlit®
The MiniSlit® machine is equipped with a bag manipulator and a belt conveyor.
View our equipment in photos
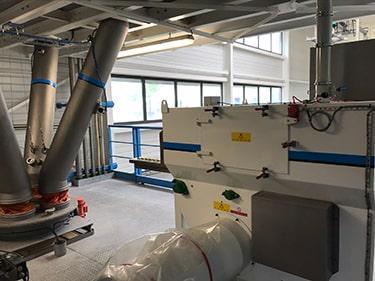
Minislit® Palamatic Process
Minislit® is an automatic bag emptying machine from Palamatic Process.
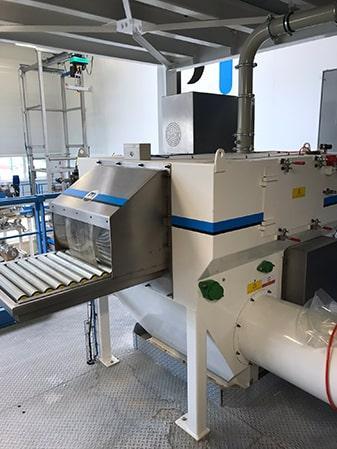
Roller conveyor Minislit®
The Minislit® system is equipped with a roller conveyor.
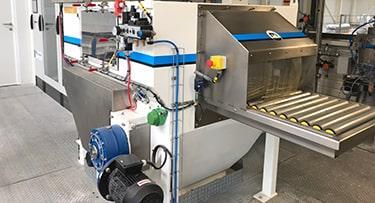
Minislit® sack discharging - Palamatic Process
The Minislit® automatic bag emptying station ensures maximum emptying rate.
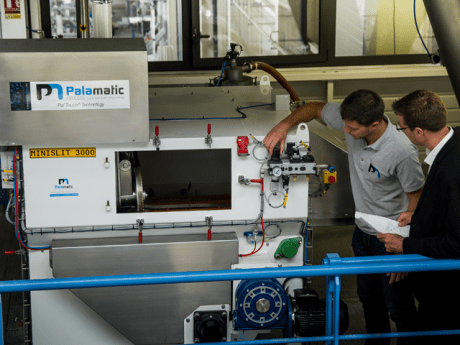
Automatic bag dump station - minislit®
Bag discharging station for bulk materials handling applications.
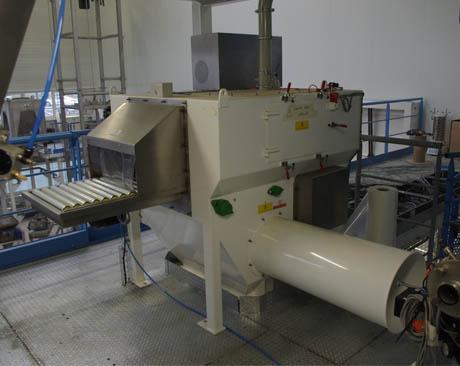
Automatic bag dump station with compactor
The screw compactor ensures the removal of empty bags and the reduction of dust emissions.
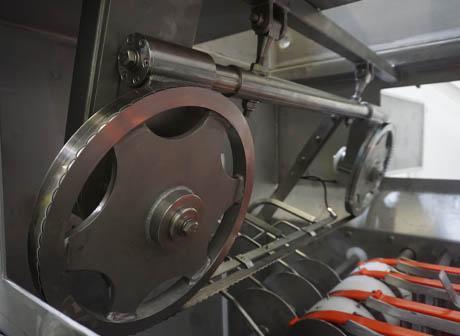
Automatic sack discharging
Inverting disc that facilitates automatic bag cutting.
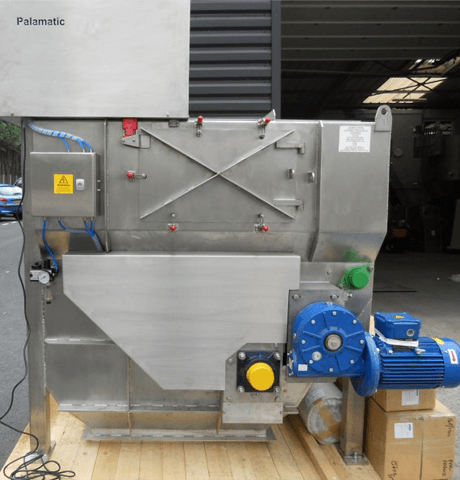
Automatic bag dump palamatic process
The Minislit® is part of our test station for easy testing with all types of bags.
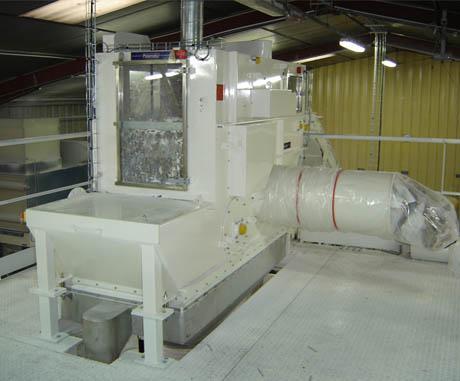
Minislit with bag compactor
Designed to open bags of powders, bulk materials, bulk solids, raw ingredients, the automatic bag discharging Minislit® is available with a strip cutting system.
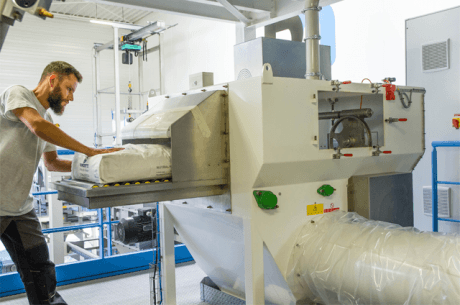
Automatic bag discharging - Minislit
The Minislit® automatic bag discharger is used to open and discharge bags made of single or multi-layer paper, polyethylene, paper with polyethylene sheath and woven plastic with or without polyethylene sheath.
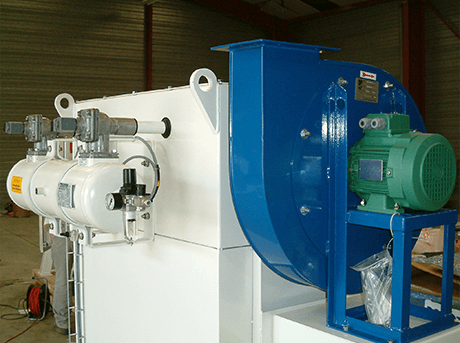
Automatic sack discharger blower
Blower system on Minislit® automatic bag discharger.
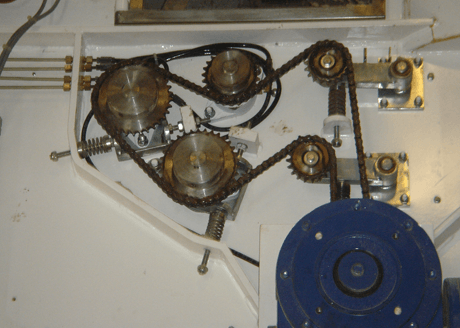
Minislit® - Palamatic Process
The mechanical drive and guide parts are installed outdoors, which protects them from wear and tear and allows very abrasive bulk materials to be discharged.
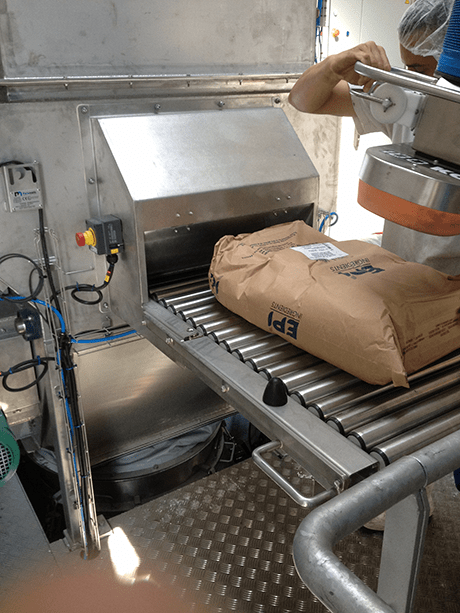
Automatic sack discharging
This gravity conveyor is fitted with 10 rollers that take the bags to the drive belts of the bag opening machine.
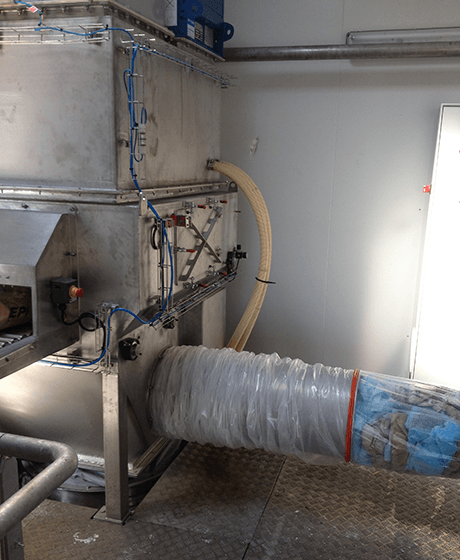
Automatic sugar sack discharging
The automatic bag dump station is connected to the pneumatic conveying.
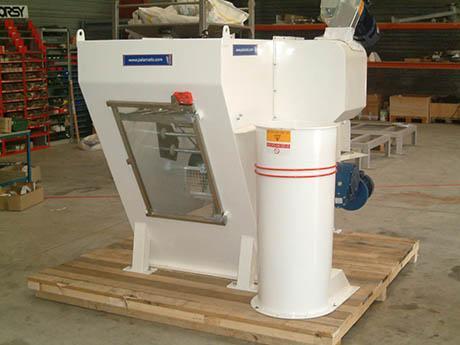
Powder processing automatic sack opening
Pneumatic ribbon cutting system available in different options: carbon steel, stainless steel or diamond coated for applications with abrasive products.
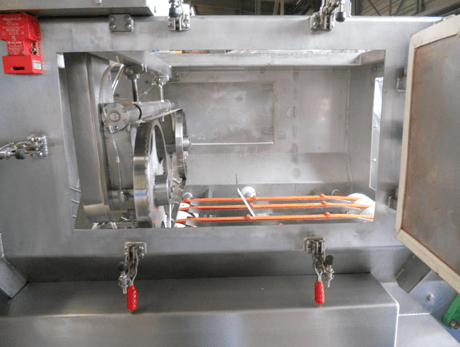
Minislit interior view
Principle of operation of the cutting system.
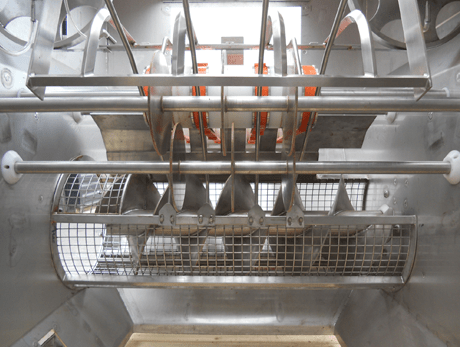
Automatic bag opening - Minislit
Automatic bag discharger for bulk solid materials, raw materials, bulk solids.
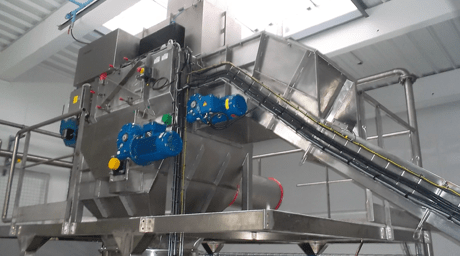
Bulk materials handling automatic sack discharging
Inclined belt for feeding the bag discharger.
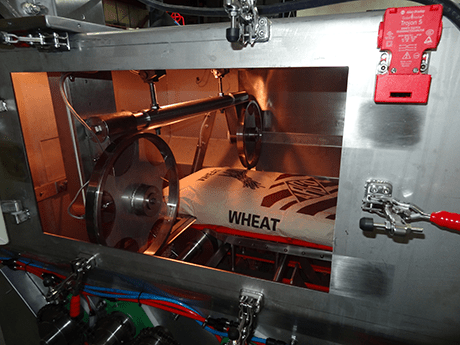
Internal view of the Minislit®
The belt conveyor transports the bag directly to the ribbon-saw cutting system.
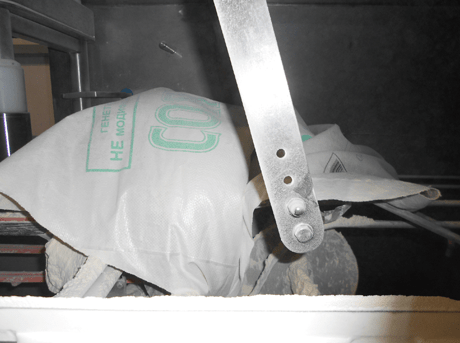
Automatic sack opening Palamatic Process
The automatic bag dump station is equipped with a belt conveyor and a bag manipulator.
Features
Technical specification
Capacity | 15 to 50 kg/sack |
---|---|
Manufacturing materials | Painted steel, 304L stainless steel, 316L stainless steel |
Electrical power | 5.5 kW |
Pneumatic consumption | 3 Nm³/h. |
Dust removal rate | 600 m³/h. |
The special profile strip cutting system without shredding allows the bags to be opened on 3 sides. The principle of turning and emptying the bags ensures a maximum emptying rate. It is particularly suitable for food and chemical industries as well as in the paint industry.
Like all PALAMATIC PROCESS bag dump stations, its design facilitates cleaning and maintenance with the minimum number of retention areas. The mechanical drive and guide parts are installed outdoors, which greatly reduces wear and tear and offers the possibility of emptying products with a high degree of abrasion.
Electrical powers | |
---|---|
Bag infeed conveyor (optional): | 1,5 kW |
Cutting head drive motor: | 1,5 kW |
Compactor and internal conveyor: | 2,2 kW |
Fan motor (optional): | 1,5 kW |
Vibrating motor (optional): | 0,25 kW |
Dimensions

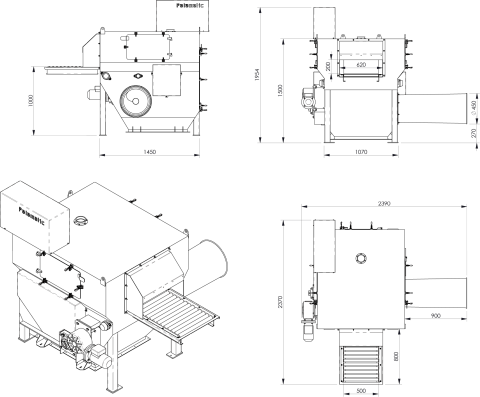
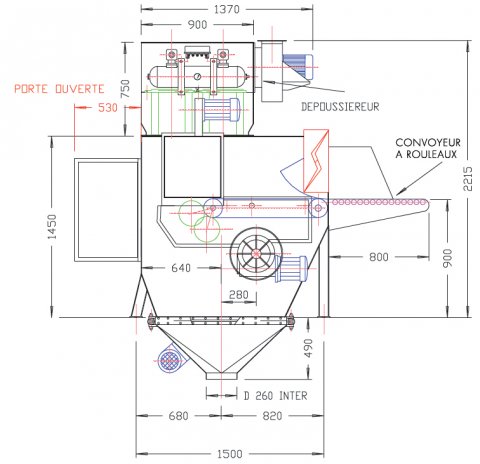
Example of implementation
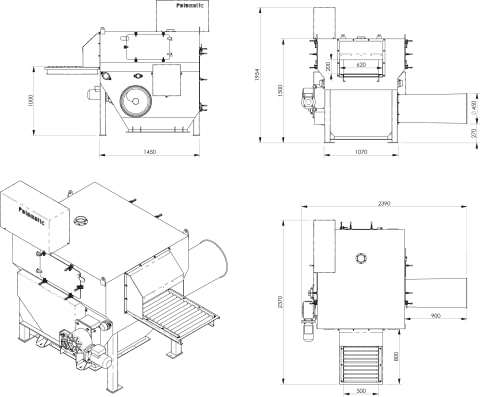
Options
Case studies
CASE STUDIES WITH THIS EQUIPMENT
Preparation of milky drink
Processed powders: milk powder and sugar - Preparation of milk drinks - Agribusiness group in the Island of Reunion, this company is a leader in most markets in which it operates: fresh dairy products...Food and Animal Feed
Compound line
Processed powder: polypropylene - Compound line - Installation of an automatic bag emptying system for polypropylene balls with a flow rate of 100 bags per hour.Chemical
Plastic extrusion
Processed powder: polypropylene - Plastic extrusion - Installation of 2 automatic bag opening machines allowing to reintroduce in the process line productions packed in 25 kg bags at a capacity of 12t...Chemical
Manufacturing line for petfood industry
Processed Powders: Soy Flour, Brewer Yeast, Corn Starch, Dried Whey... - Manufacturing line for petfood industry - Manufacturering of dry and liquid flavor enhancers for the pet food industryFood and Animal Feed