Processed powders: milk powder and sugar
Preparation of milky drink
Agribusiness group in the Island of Reunion, this company is a leader in most markets in which it operates: fresh dairy products, UHT milk, soft drinks, ice creams and traditional cheeses.
Optimize the automatic unloading of milk powders contained in bags and sugar contained in bulk bags (Big bag discharging - Stripping box - Easyflow EF0).
Due to 2 different unloading systems, Palamatic Process intervened on two separate installations: one to handle sugar (Bulk bag unloader) and one to handle milk powder (Automatic bag opener Minislit).
Sugar working station:
The client wished a re-design of the existing bulk bag unloader for the deconditioning of sugar delivered in bulk bags.
To facilitate the flow of the bulk materials, massage cylinders have been positioned on either side of the bulk bag to exert pressure which helps the sugar to flow down.
Load cells have also been installed on the structure for a better control of the unloading process and the buffer hopper has a connection to the dust collector integrated in the automatic bag opener Minislit®.
The powder is then conveyed through a trough screw fitted with a cover with hinges to a vibrating screener separator which aims to eliminate all foreign bodies potentially present.
Once the material is free from any foreign bodies, it goes through a drop through rotary airlock valve in a gravity manner and is then conveyed to the vacuum conveying system.
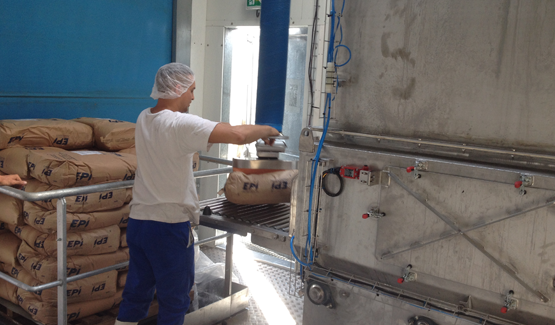
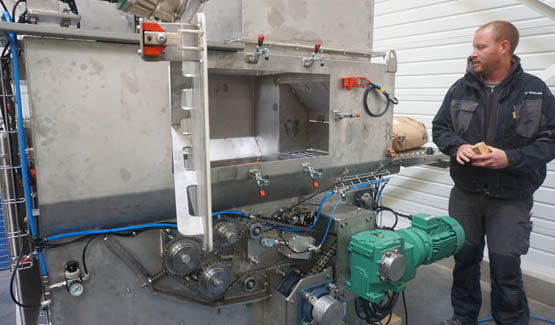
Dairy powder system:
Dairy powder is packed in small sacks that are stored on a pallet for a total weight of one ton.
The goal of our customer was to increase the ergonomics of the work station and the discharge rate of the sacks, with the goal of 6 bags per minute.
Palamatic Process designed a hydraulic lifting table for the pallets of dairy powder sacks to meet the constraints of the site's floor layout. To assist in the ergonomics of operator sack loading, a vacuum bag lifter provides the means to lift and deposit the sacks on the polyurethane belt conveyor that feeds the automatic bag opener Minislit®.
Sensors detect the entry of the sack into the auto opener, which triggers the cutting system. The saw blade cuts the bag and the lower part of the bag material is gripped by rotating discs. Thanks to the reversing disc system, the bag is turned over for a complete discharge of the contents. The bag waste is then dropped and evacuated by an integrated bag compactor. When the sensor is disabled, the blade goes back to its resting position.
The dairy powder drops into a vibrating screener - GSC 900 with a 4 mm mesh that is connected to the automatic bag opener Minislit® by a flexible sleeve. The powder then falls into a drop through rotary airlock valve to be transferred to the pneumatic conveying station.