1. Main characteristics of starch
Starch is a complex carbohydrate made up of sugar. It is present in several plants such as seeds (cereals, legumes), roots, tubers and rhizomes (potato, cassava), fruits (banana). It results from the mixture of two homopolymers: amylose and amylopectin.
Starch is a biodegradable element.
Starch takes the form of an odorless white powder. The starch grain has the appearance of semi-crystalline granules.
Its density is equal to 1.5 g / cm³. It dissolves in water, ethanol, and pyridine, but not in organic solvents.
2. Main applications of starch
Starch has many fields of application.
In the food industry, it is used in drinks, confectionery, ready-made meals, as well as in baking. Starch from cereals is used to make sweeteners such as syrups (malted barley, corn, brown rice, etc.). Pea starch also has a texturizing power, especially for the production of sauces and creams.
In the chemical industry, it fulfills several functions: - Bleaching, coating and glue (paper and cardboard industries) - Excipient and tablet film coating (pharmaceutical industry) - Fermentation for the production of bioethanol
Starch is also used in the manufacture of cosmetics, detergents, construction materials and adhesives.
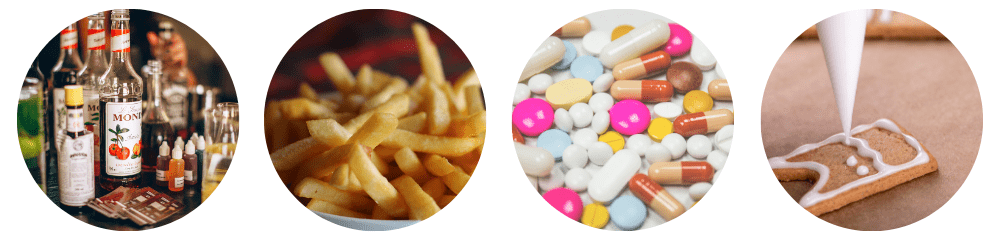
3. Industrial handling of starch
Depending on the nature and origin of the starch (starch from seeds, roots, tubers, etc.), its flow properties will vary. Its degree of humidity will also affect the fluidity of the starch powder (the higher it is, the more lumps can form and block certain equipment).
Starch should be kept away from all sources of ignition and should not be exposed to high temperatures. Starch powder presents an explosive hazard if mixed with air. It is therefore essential to avoid the accumulation of dust and to choose equipment adapted to this specificity.
Starch should be stored in an airtight, ventilated, cool and dry place.
4. Starch applications with Palamatic Process equipment
Starch has many operations in the industrial environment. It can be packaged in bulk bags or sacks, emptied, dosed, crushed, transported or even stored.
In general, any starch packaging line consists of a weighing system and / or a bagging machine. During this filling phase, special attention must be paid to hygiene and sealing so that no starch dust emissions take place in your workshop. The Palamatic Process Palsack® 01 filling station, made of stainless steel, is equipped with a sealing system ensuring total containment of your process. It allows you to fill all types of open mouth bags and automate weighing management.
Starch can also be unloaded from sacks or bulk bags. The EasyFlow® EF0 bulk bag emptying station (electric hoist loading), designed in 304 stainless steel, allows the starch to flow out of the big bag using massage jacks. The starch can then be stored in a buffer hopper located below the EasyFlow® station. Empty bulk bags can be compressed and stored in a polyethylene sheath using a bulk bag compactor.
To transfer the starch powder, a pneumatic vacuum conveying system, like our VFlow® model, can be implemented.
Vibro-fluidizers facilitating the flow of the starch powder can also be added to the line.
The bulk bag filling line from the TruckFlow® 06 tanker truck, developed by Palamatic, is ideal for packaging starch powder.
In order to guarantee operators a healthy working atmosphere, a de-dusting system can further be integrated in the process line.
5. Palamatic Process customer applications with starch
Palamatic Process has been assisting starch manufacturers in their production process for more than 30 years. A number of installations handling starch powder are currently in operation. Here are some examples of achievements:
- Grinding unit for icing sugar production and incorporation of starch anti-caking agents.
- Starch dosed feeder for ready meal production line.
- Starch unloading from truck for automatic packaging of big bags in ATEX zone.
- Food additive dosing line with cleaning in place of all the equipment.
Our experts are ATEX certified and are available to analyse your powders and propose suitable equipment to optimise your production. Contact us to make an appointment.